University certificate
The world's largest faculty of engineering”
Why study at TECH?
Access a Professional master’s degree of the highest level and master Mechatronics Engineering from the best experts with TECH"
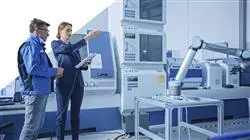
The technology industry is advancing by leaps and bounds. Every year millions of dollars are invested in this sector, a small figure compared to the benefits it brings. One of the emerging focuses that has generated the greatest impact has been
Mechatronics Engineering, especially for the versatility it encompasses, as well as for the wide range of applications and challenges it proposes. In short: it has become an endless opportunity for innovation. However, it is also a challenge for all professionals, especially because of the dizzying pace at which mechanics, electronics and computer science are advancing in the design of intelligent systems and products.
In view of this, TECH has developed this Professional master’s degree in Mechatronics Engineering, a complete and comprehensive program that brings together the advances in this field in 1,500 hours of the best theoretical, practical and additional content. This is an unparalleled academic experience with which the professionals will be able to delve into the interdisciplinary nature of this area, learning the most effective techniques and methods for system design, axis control, automation or numerical simulation. In addition, students will be able to delve into the assisted manufacturing of components, being updated on the latest developments of the most effective materials in the current engineering market.
All this over 12 months, during which you will have unlimited access to a state-of-the-art virtual platform, without schedules or on-site classes, offering you an academic experience that adapts to your total and absolute availability. In addition, it is supported by a convenient 100% online format, as well as the Relearningmethodology, aspects that have allowed TECH to position itself as the best digital university in the world. It is, therefore, a unique opportunity to begin a program that will raise the knowledge and talent of the engineer to the highest level in an area in expansion and with great expectations for the future, such as Mechatronics Engineering.
After the course of this Professional master’s degree you will stand out for your exhaustive handling of electronics and mechanics in less than 12 months"
This Professional master’s degree in Mechatronics Engineering contains the most complete and up-to-date program on the market. The most important features include:
- The development of case studies presented by experts in computer engineering and technology
- The graphic, schematic and practical contents of the book provide technical and practical information on those disciplines that are essential for professional practice
- Practical exercises where the self-assessment process can be carried out to improve learning
- Its special emphasis on innovative methodologies
- Theoretical lessons, questions to the expert, debate forums on controversial topics, and individual reflection assignments
- Content that is accessible from any fixed or portable device with an Internet connection
Master the best instrumentation strategies by delving into the development of controlled variables in today's computer environment"
The program’s teaching staff includes professionals from the field who contribute their work experience to this educational program, as well as renowned specialists from leading societies and prestigious universities.
The multimedia content, developed with the latest educational technology, will provide the professional with situated and contextual learning, i.e., a simulated environment that will provide immersive education programmed to learn in real situations.
This program is designed around Problem-Based Learning, whereby the professional must try to solve the different professional practice situations that arise during the academic year For this purpose, the students will be assisted by an innovative interactive video system created by renowned and experienced experts.
Implement to your skills the exhaustive management of the most advanced techniques in product design and prototyping with TECH"
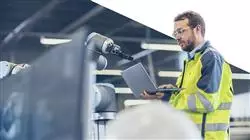
More than 1,500 hours of the best theoretical, practical and additional content compacted in a convenient 100% online format"
Syllabus
Both the development of the content and the structuring of this Professional master’s degree were the responsibility of the teaching team. Thanks to this, it has been possible to create a program of the highest level consisting of more than 1,000 hours of the best theoretical, practical and additional content compacted in a convenient 100% online format. Graduates will be able to expand their knowledge in Mechatronics Engineering in an adapted way, allowing them to learn in detail the latest developments in integration, development and manufacturing from wherever they want and with a schedule fully adapted to their availability.
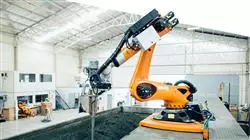
Connect from wherever you want and whenever you want through a program that adapts to your needs"
Module 1. Mechatronics Machines and Systems
1.1. Motion transformation systems
1.1.1. Complete circular transformation: reciprocating circular
1.1.2. Full circular transformation: continuous rectilinear
1.1.3. Intermittent motion
1.1.4. Straight line mechanisms
1.1.5. Stopping mechanisms
1.2. Machines and mechanisms: motion transmission
1.2.1. Linear motion transmission
1.2.2. Circular motion transmission
1.2.3. Transmission of flexible elements: belts and chains
1.3. Machine stresses
1.3.1. Static stresses
1.3.2. Failure criteria
1.3.3. Fatigue in machines
1.4. Gears
1.4.1. Types of gears and manufacturing methods
1.4.2. Geometry and kinematics
1.4.3. Gear trains
1.4.4. Force analysis
1.4.5. Gear strength
1.5. Shafts
1.5.1. Stresses in shafts
1.5.2. Design of shafts and axles
1.5.3. Rotodynamics
1.6. Bearings
1.6.1. Types of rolling bearings
1.6.2. Bearing calculation
1.6.3. Selection Criteria
1.6.4. Mounting, lubrication and maintenance techniques
1.7. Springs
1.7.1. Types of springs
1.7.2. Helical springs
1.7.3. Energy storage by means of springs
1.8. Mechanical connecting elements
1.8.1. Types of joints
1.8.2. Design of Non-Permanent Joints
1.8.3. Design of Permanent Connections
1.9. Transmissions by means of flexible elements
1.9.1. Straps
1.9.2. Roller chains
1.9.3. Wire ropes
1.9.4. Flexible shafts
1.10. Brakes and clutches
1.10.1. Types of brakes/clutches
1.10.2. Friction materials
1.10.3. Calculation and sizing of clutches
1.10.4. Brake calculation and sizing
Module 2. Assisted manufacturing of mechanical components in mechatronic systems
2.1. Mechanical manufacturing in mechatronic systems
2.1.1. Mechanical manufacturing technologies
2.1.2. Mechanical manufacturing in the mechatronics industry
2.1.3. Advances in mechanical manufacturing in the mechatronics industry
2.2. Material removal processes
2.2.1. Theory of metal cutting
2.2.2. Traditional machining processes
2.2.3. CNC and automation in manufacturing
2.3. Sheet metal forming technologies
2.3.1. Sheet metal cutting technologies: laser, water and plasma
2.3.2. Technology selection criteria
2.3.3. Sheet metal bending
2.4. Abrasion processes
2.4.1. Manufacturing techniques by abrasion
2.4.2. Abrasive tools
2.4.3. Shot blasting and sandblasting processes
2.5. Advanced technologies in mechanical manufacturing
2.5.1. Additive manufacturing and its applications
2.5.2. Micro-manufacturing and nanotechnology
2.5.3. Electrical discharge machining
2.6. Rapid prototyping techniques
2.6.1. 3D printing in rapid prototyping
2.6.2. Rapid prototyping applications
2.6.3. 3D printing solutions
2.7. Design for manufacturing in mechatronic systems
2.7.1. Manufacturing-oriented design principles
2.7.2. Topological optimization
2.7.3. Design innovation for manufacturing in mechatronics systems
2.8. Plastic forming technologies
2.8.1. Injection molding processes
2.8.2. Blow molding
2.8.3. Compression and transfer molding
2.9. Advanced technologies in plastic forming
2.9.1. Metrology
2.9.2. Units of measurement and international standards
2.9.3. Measuring instruments and tools
2.9.4. Advanced metrology techniques
2.10. Quality Control
2.10.1. Measuring methods and sampling techniques
2.10.2. Statistical Process Control (SPC)
2.10.3. Regulations and quality standards
2.10.4. Total Quality Management (TQM)
Module 3. Sensors and Actuators
3.1. Sensors
3.1.1. Sensor Selection
3.1.2. Sensors in mechatronic systems
3.1.3. Application Examples
3.2. Presence or proximity sensors
3.2.1. Limit switches: principle of operation and technical characteristics
3.2.2. Inductive detectors: operating principle and technical characteristics
3.2.3. Capacitive detectors: principle of operation and technical characteristics
3.2.4. Optical detectors: principle of operation and technical characteristics
3.2.5. Ultrasonic detectors: operating principle and technical characteristics
3.2.6. Selection Criteria
3.2.7. Application Examples
3.3. Position sensors
3.3.1. Incremental encoders: principle of operation and technical characteristics
3.3.2. Absolute encoders: principle of operation and technical characteristics
3.3.3. Laser sensors: principle of operation and technical characteristics
3.3.4. Magnetostrictive sensors and linear potentiometers
3.3.5. Selection Criteria
3.3.6. Application Examples
3.4. Temperature Sensors
3.4.1. Thermostats: operating principle and technical characteristics
3.4.2. Resistance thermometers: principle of operation and technical characteristics
3.4.3. Thermocouples: principle of operation and technical characteristics
3.4.4. Radiation pyrometers: principle of operation and technical characteristics
3.4.5. Selection Criteria
3.4.6. Application Examples
3.5. Sensors for the measurement of physical variables in processes and machines
3.5.1. Pressure operating principle
3.5.2. Flow rate: operating principle
3.5.3. Level: operating principle
3.5.4. Sensors for Other Physical Variables
3.5.5. Selection Criteria
3.5.6. Application Examples
3.6. Actuators
3.6.3. Actuator selection
3.6.4. Actuators in mechatronic systems
3.6.5. Application Examples
3.7. Electric actuators
3.7.1. Relays and contactors: principle of operation and technical characteristics
3.7.2. Rotary motors: principle of operation and technical characteristics
3.7.3. Stepper motors: operating principle and technical characteristics
3.7.4. Servomotors: principle of operation, technical characteristics
3.7.5. Selection Criteria
3.7.6. Application Examples
3.8. Pneumatic actuators
3.8.1. Valves and servovalves principle of operation and technical characteristics
3.8.2. Pneumatic cylinders: principle of operation and technical characteristics
3.8.3. Pneumatic motors: operating principle and technical characteristics
3.8.4. Vacuum clamping: working principle and technical characteristics
3.8.5. Selection Criteria
3.8.6. Application Examples
3.9. Hydraulic actuators
3.9.1. Valves and servovalves principle of operation and technical characteristics
3.9.2. Hydraulic cylinders: principle of operation and technical characteristics
3.9.3. Hydraulic motors: operating principle and technical characteristics
3.9.4. Selection Criteria
3.9.5. Application Examples
3.10. Example of application of sensor and actuator selection in machine design
3.10.1. Description of the machine to be designed
3.10.2. Sensor Selection
3.10.3. Actuator selection
Module 4. Design of mechatronic systems
4.1. CAD in engineering
4.1.1. CAD in engineering
4.1.2. 3D Parametric Design
4.1.3. Types of software on the market
4.1.4. SolidWorks. Inventor
4.2. Work Environment
4.2.1. Work Environment
4.2.2. Menus
4.2.3. Visualization
4.2.4. Default settings of the working environment
4.3. Layout and work structure
4.3.1. 3D computer-aided design
4.3.2. Parametric design methodology
4.3.3. Methodology for the design of assemblies of parts. Assemblies
4.4. Sketching
4.4.1. Basics of Sketch design
4.4.2. 2D Sketch Creation
4.4.3. Sketch editing tools
4.4.4. Sketch dimensioning and relationships
4.4.5. 3D Sketch Creation
4.5. Mechanical design operations
4.5.1. Mechanical design methodology
4.5.2. Mechanical design operations
4.5.3. Other operations
4.6. Surfaces
4.6.1. Creating surfaces
4.6.2. Tools for creating surfaces
4.6.3. Tools for surface editing
4.7. Assemblies
4.7.1. Creation of assemblies
4.7.2. The relationships in position
4.7.3. Tools for the creation of assemblies
4.8. Normalization and design tables. Variables
4.8.1. Component library. Toolbox
4.8.2. Online repositories/element manufacturers
4.8.3. Design tables
4.9. Folded sheet metal
4.9.1. Folded sheet metal module in CAD software
4.9.2. Sheet metal operations
4.9.3. Developments for sheet metal cutting
4.10. Drawing generation
4.10.1. Creation of drawings
4.10.2. Drawing Formats
4.10.3. Creation of views
4.10.4. Dimensioning
4.10.5. Annotations
4.10.6. Lists and tables
Module 5. Axis control, mechatronic systems and automation
5.1. Automation of production processes
5.1.1. Automation of production processes
5.1.2. Classification of control systems
5.1.3. Technologies used
5.1.4. Machine automation and/or process automation
5.2. Mechatronic systems: elements
5.2.1. Mechatronic systems
5.2.2. The programmable logic controller as a discrete process control element
5.2.3. The controller as a control element for continuous process control
5.2.4. Axis and robot controllers as position control elements
5.3. Discrete control with programmable logic controllers (PLC's)
5.3.1. Hardwired logic vs. programmed logic
5.3.2. Control with PLC's
5.3.3. Field of application of PLCs
5.3.4. Classification of PLCs
5.3.5. Selection Criteria
5.3.6. Application Examples
5.4. PLC programming
5.4.1. Representation of control systems
5.4.2. Cycle of operation
5.4.3. Configuration possibilities
5.4.4. Variable identification and address assignment
5.4.5. Programming Languages
5.4.6. Instruction set and programming software
5.4.7. Programming example
5.5. Methods of describing sequential drives
5.5.1. Design of sequential drives
5.5.2. GRAFCET as a method for describing sequential drives
5.5.3. Types of GRAFCET
5.5.4. GRAFCET elements
5.5.5. Standard symbology
5.5.6. Application Examples
5.6. Structured GRAFCET
5.6.1. Structured design and programming of control systems
5.6.2. Modes of operation
5.6.3. Security/Safety
5.6.4. Hierarchical GRAFCET diagrams
5.6.5. Structured design examples
5.7. Continuous control by means of controllers
5.7.1. Industrial controllers
5.7.2. Scope of application of the regulators. Classification
5.7.3. Selection Criteria
5.7.4. Application Examples
5.8. Machine Automation
5.8.1. Machine Automation
5.8.2. Speed and position control
5.8.3. Safety systems
5.8.4. Application Examples
5.9. Position control by axis control
5.9.1. Position control
5.9.2. Field of application of axis controllers. Classification
5.9.3. Selection Criteria
5.9.4. Application Examples
5.10. Example of application of equipment selection in machine design
5.10.1. Description of the machine to be designed
5.10.2. Equipment selection
5.10.3. Resolved application
Module 6. Structural calculation of mechanical systems and components
6.1. Finite Element Method
6.1.1. The Finite Element Method
6.1.2. Discretization and mesh convergence
6.1.3. Shape functions. Linear and quadratic elements
6.1.4. Formulation for bars. Stiffness matrix method
6.1.5. Nonlinear problems. Sources of nonlinearity. Iterative methods
6.2. Linear static analysis
6.2.1. Preprocessing: geometry, material, mesh, boundary conditions: forces, pressures, remote loads
6.2.2. Solution
6.2.3. Post-processing: stress and strain maps
6.2.4. Application Examples
6.3. Geometry preparation
6.3.1. Types of import files
6.3.2. Geometry preparation and cleaning
6.3.3. Conversion to surfaces and beams
6.3.4. Application Examples
6.4. Mesh
6.4.1. One-dimensional, two-dimensional, three-dimensional elements
6.4.2. Mesh control parameters: local meshing, mesh growth
6.4.3. Meshing methodologies: structured meshing, swept meshing
6.4.4. Mesh quality parameters
6.4.5. Application Examples
6.5. Material modeling
6.5.1. Elastic-linear materials
6.5.2. Elasto-plastic materials. Plasticity criteria
6.5.3. Hyperelastic materials. Models in isotropic hyperelasticity: Mooney Rivlin, Yeoh, Ogden, Arruda-Boyce
6.5.4. Application Examples
6.6. Contact
6.6.1. Linear contacts
6.6.2. Non-linear contacts
6.6.3. Formulations for contact resolution: Lagrange, Penalty
6.6.4. Preprocessing and postprocessing of the contact
6.6.5. Application Examples
6.7. Connectors
6.7.1. Bolted Joints
6.7.2. Beams
6.7.3. Kinematic torques: rotation and translation
6.7.4. Example of Application. Loads on connectors
6.8. Solver. Solving the problem
6.8.1. Solving parameters
6.8.2. Convergence and definition of residuals
6.8.3. Application Examples
6.9. Post-Process
6.9.1. Stress and deformation mappings. Isosurfaces
6.9.2. Forces in connectors
6.9.3. Safety coefficients
6.9.4. Application Examples
6.10. Vibration analysis
6.10.1. Vibrations: stiffness, damping, resonance
6.10.2. Free vibrations and forced vibrations
6.10.3. Time domain or frequency domain analysis
6.10.4. Application Examples
Module 7. Robotics applied to Mechatronic Engineering
7.1. The Robot
7.1.1. The Robot
7.1.2. Robot applications
7.1.3. Classification of Robots
7.1.4. Mechanical structure of a robot
7.1.5. Specifications of a robot
7.2. Technological Components
7.2.1. Electric, pneumatic and hydraulic actuators
7.2.2. Sensors internal and external to the robot
7.2.3. Vision Systems
7.2.4. Selection of motors and sensors
7.2.5. Terminal elements and grippers
7.3. Transformations
7.3.1. Robot architecture
7.3.2. Position and orientation of a solid
7.3.3. Euler orientation angles
7.3.4. Homogeneous transformation matrices
7.4. Kinematics of position and orientation
7.4.1. Denavit-Hartenberg formulation
7.4.2. Direct Kinematic Problem
7.4.3. Inverse Kinematic Problem
7.5. Kinematics of velocities and accelerations
7.5.1. Velocity and acceleration of a solid
7.5.2. Jacobian matrix
7.5.3. Singular configurations
7.6. Statics
7.6.1. Force and moment equilibrium equations
7.6.2. Calculation of statics. Recursive method
7.6.3. Static analysis using the Jacobian matrix
7.7. Dynamics
7.7.1. Dynamic properties of a solid
7.7.2. Newton-Euler formulation
7.7.3. Lagrange-Euler formulation
7.8. Kinematic control
7.8.1. Trajectory planning
7.8.2. Interpolators in joint space
7.8.3. Trajectory planning in Cartesian space
7.9. Monoarticular linear dynamic control
7.9.1. Control Techniques
7.9.2. Dynamic systems
7.9.3. Transfer function model and state space representation
7.9.4. Dynamic model of a DC motor
7.9.5. Control of a d.c. motor
7.10. Programming
7.10.1. Programming systems
7.10.2. Programming Languages
7.10.3. Programming techniques
Module 8. Numerical simulation of mechanical systems
8.1. Rigid Solid Mechanics
8.1.1. Plane mechanics of rigid solids
8.1.2. 3D Orientation
8.1.3. Three-dimensional mechanics of the rigid solid
8.2. Multibody systems
8.2.1. Multibody systems
8.2.2. Mobility and degrees of freedom
8.2.3. Kinematic torques, types and effects
8.2.4. Redundancy of constraints
8.3. Kinematics of multibody systems
8.3.1. Motion with constraints
8.3.2. Initial position problem
8.3.3. Newton-Raphson method
8.3.4. Finite displacement
8.4. Velocity and acceleration in multibody systems
8.4.1. Jacobian matrix
8.4.2. Direct kinematics
8.4.3. Inverse Kinematics
8.5. Advanced tools for the study of 3D system kinematics
8.5.1. Kinematic relations in 3D
8.5.2. Transformation matrices
8.5.3. The Denavit Hartenberg representation
8.6. General dynamics of multibody systems
8.6.1. Newton-Euler equations
8.6.2. Lagrange Equations
8.6.3. Constraint equations
8.7. Simulation tools for multibody systems
8.7.1. Simulation by means of explicit and implicit methods
8.7.2. Euler methods
8.7.3. Runge-Kutta family of methods
8.7.4. Stability and accuracy
8.8. Contact and collision detection
8.8.1. Contact models
8.8.2. Penalty models
8.8.3. Implementation of the contact problem in simulation
8.9. Simulation of flexible elements
8.9.1. Kinematics of deformable solids
8.9.2. Equilibrium equations
8.9.3. Principle of virtual works
8.10. Optimization tools applied to multibody systems
8.10.1. Optimization problem formulation
8.10.2. Optimization methods applied to multibody systems
8.10.3. Synthesis of mechanisms through optimization
Module 9. Embedded Systems
9.1. Embedded systems in engineering
9.1.1. Embedded systems
9.1.2. Embedded systems in engineering
9.1.3. Importance of embedded systems in modern engineering
9.2. Microcontrollers
9.2.1. Microcontrollers
9.2.2. Differences between microcontrollers and development boards
9.2.3. Microcontrollers and development boards
9.2.4. Programming languages for microcontrollers
9.3. Sensors and Actuators
9.3.1. Industrial sensors
9.3.2. Industrial actuators
9.3.3. Communication between sensors and the central unit
9.3.4. Actuator Control in Embedded Systems
9.4. Embedded Systems for Real-Time Control
9.4.1. Hard real time system (hard real time)
9.4.2. Soft real time systems (soft real time)
9.4.3. Programming of real time systems
9.5. Embedded digital signal processing systems
9.5.1. Digital Signal Processing (DSP)
9.5.2. Design of DSP algorithms in embedded systems
9.5.3. Applications of DSP in engineering by means of embedded systems
9.6. Programmable hardware in embedded systems
9.6.1. Programmable Logic and FPGAs
9.6.2. Design of logic circuits in programmable hardware
9.6.3. Programmable hardware technologies
9.7. Single Board Computers (SBC)
9.7.1. Parts of single board computers
9.7.2. Main architectures
9.7.3. Single-board computers vs. desktop computers
9.8. Embedded Systems in the Internet of Things (IoT)
9.8.1. Internet of things (IoT)
9.8.2. Integration of Embedded Systems in the IoT
9.8.3. Sensors and IoT Devices
9.8.4. Use cases and practical applications
9.9. Security and reliability in embedded systems
9.9.1. Threats and Vulnerabilities in Embedded Systems
9.9.2. Secure design and coding practices
9.9.3. Maintenance and security updates
9.10. Embedded Systems Communication and Connectivity
9.10.1. Communication Protocols for Embedded Systems
9.10.2. Sensor networks and wireless communication
9.10.3. Integration with the Internet and the cloud
Module 10. Mechatronic Systems Integration
10.1. Integrated manufacturing systems
10.1.1. Integrated manufacturing systems
10.1.2. Industrial communications in systems integration
10.1.3. Integration of control equipment in the production processes
10.1.4. New production paradigm: Industry 4.0
10.2. Industrial communication networks
10.2.1. Industrial communications. Evolution
10.2.2. Structure of industrial networks
10.2.3. Current situation of industrial communications
10.3. Communication networks at the process interface level
10.3.1. AS-i: elements
10.3.2. IO-Link: elements
10.3.3. Integration of equipment
10.3.4. Selection Criteria
10.3.5. Application Examples
10.4. Communication networks at the control and regulation level
10.4.1. Communication networks at the command and control level
10.4.2. Profibus: elements
10.4.3. Canbus: elements
10.4.4. Equipment integration
10.4.5. Selection Criteria
10.4.6. Application Examples
10.5. Communication networks at centralized supervisory and command level
10.5.1. Centralized supervisory and command level networks
10.5.2. Profinet: elements
10.5.3. Ethercat: elements
10.5.4. Equipment integration
10.5.5. Application Examples
10.6. Process monitoring and control systems
10.6.1. Process monitoring and control systems
10.6.2. Human Machine Interfaces (HMIs)
10.6.3. Examples of use
10.7. Operator panels
10.7.1. The operator panel as a human-machine interface
10.7.2. Membrane panels
10.7.3. Touch panels
10.7.4. Communication possibilities of the operator panels
10.7.5. Selection Criteria
10.7.6. Application Examples
10.8. SCADA Packages
10.8.1. SCADA packages as man-machine interface
10.8.2. Selection Criteria
10.8.3. Application Examples
10.9. Industry 4.0. Intelligent manufacturing
10.9.1. Industry 4.0
10.9.2. Architecture of the new factories
10.9.3. Industry 4.0 technologies
10.9.4. Examples of manufacturing based on Industry 4.0
10.10. Example of application of equipment integration in an automated process
10.10.1. Description of the process to be automated
10.10.2. Selection of control equipment
10.10.3. Integration of equipment
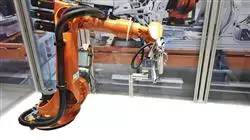
Access over 1,000 hours of multidisciplinary content and revolutionize Mechatronics Engineering with the most advanced and up-to-date knowledge in the industry”
Professional Master's Degree in Mechatronics Engineering
Mechatronics engineering is a highly interdisciplinary discipline that combines mechanics, electronics, computer science and robotics to design or develop intelligent and automated systems and products. Are you ready to take the next step in your career and specialize in this field? If you are passionate about technology, automation and innovation, this Professional Master's Degree in Mechatronics Engineering created by TECH Global University is the gateway to a world of exciting opportunities. In this program, taught in online mode, you will prepare you to lead multidisciplinary projects and create intelligent solutions in an increasingly automated environment. To make this training a unique and easily accessible experience, we have structured all classes in a 100% online format, where you will be able to flexibly schedule them according to your needs and have at your disposal state-of-the-art multimedia content.
Study at the world's largest online engineering school
Mechatronics engineering combines mechanics, electronics, computer science and robotics. Our program encompasses all of these areas, giving you comprehensive training and versatile skills to excel in industry. The demand for mechatronics engineers is constantly growing. With this program, you'll be ready to take on leadership roles in a variety of industries, from automotive to manufacturing. The foundations of this Professional Master's Degree were designed with the best methodologies specialized in online learning, this will facilitate the development of your course in a completely autonomous and practical way; to receive your lessons you will only need to have a device connected to the internet. Enroll today and shape your future, take advantage of the opportunity to train in one of the most exciting and promising fields of engineering. Our Professional Master's Degree will prepare you to lead the technological revolution and make a difference in the world of automation. Enroll now and start your journey to a successful career in mechatronics engineering!
.