University certificate
The world's largest faculty of engineering”
Introduction to the Program
A 100% online Postgraduate diploma with which you will master the monoarticular linear control systems implemented in Robotics"
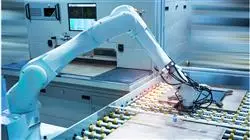
Robotics has had a great impact that has allowed it to be introduced in many professional sectors. Its use brings multiple benefits such as increased productivity, efficiency and profitability of companies. For this reason, more and more companies are demanding expert profiles in robotics to add these technologies to their production processes.
In view of this reality, TECH has designed a study program that delves into the main advances in Industrial Robotics. In particular, its syllabus includes an exhaustive analysis of the automation, control and regulation systems involved in this type of technology. At the same time, it deals with the fundamental temperature and pressure sensors, as well as the most advanced pneumatic and hydraulic actuators in this field of Mechatronics.
On the other hand, the academic itinerary covers the classification and specific applications of robots. It also delves into the dynamics, statics and kinematic control of these complex machines. At the same time, it allows the student to master programming languages and the most disruptive techniques to establish direct communication with automated equipment.
From the didactic point of view, engineers have the exclusive seal of TECH 100% online methodology. This provides them with rigorous study materials based on the latest scientific evidence, as well as various multimedia resources such as explanatory videos and interactive summaries. In addition, this Postgraduate diploma is not governed by hermetic schedules, nor does it require any unnecessary travel. For this reason, completing this syllabus constitutes a comfortable and flexible academic experience, as well as a demanding one.
Get up to date with this program about the main technological components and mechanical structures that make up a robot"
This Postgraduate diploma in Industrial Robotics contains the most comprehensive and up-to-date program on the market. Its most notable features are:
- The development of case studies presented by experts in Industrial Robotics.
- The graphic, schematic and practical contents with which it is conceived provide cutting- Therapeutics and practical information on those disciplines that are essential for professional practice.
- Practical exercises where the self-assessment process can be carried out to improve learning
- Its special emphasis on innovative methodologies
- Theoretical lessons, questions to the expert, debate forums on controversial topics, and individual reflection assignments
- Content that is accessible from any fixed or portable device with an Internet connection
Thanks to TECH you will handle the most advanced software and programming languages of the Robotics Industry"
The program’s teaching staff includes professionals from the field who contribute their work experience to this educational program, as well as renowned specialists from leading societies and prestigious universities.
The multimedia content, developed with the latest educational technology, will provide the professional with situated and contextual learning, i.e., a simulated environment that will provide immersive education programmed to learn in real situations.
This program is designed around Problem-Based Learning, whereby the professional must try to solve the different professional practice situations that arise during the academic year For this purpose, the students will be assisted by an innovative interactive video system created by renowned and experienced experts.
TECH, the best digital university in the world according to Forbes, will guarantee you a 100% online methodology, adapted to your needs and schedules"
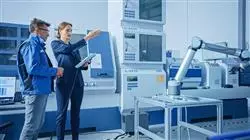
Enroll now and you will go deeper into the methods of describing sequential automatisms"
Why study at TECH?
TECH is the world’s largest online university. With an impressive catalog of more than 14,000 university programs available in 11 languages, it is positioned as a leader in employability, with a 99% job placement rate. In addition, it relies on an enormous faculty of more than 6,000 professors of the highest international renown.
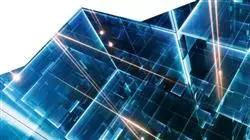
Study at the world's largest online university and guarantee your professional success. The future starts at TECH”
The world’s best online university according to FORBES
The prestigious Forbes magazine, specialized in business and finance, has highlighted TECH as “the world's best online university” This is what they have recently stated in an article in their digital edition in which they echo the success story of this institution, “thanks to the academic offer it provides, the selection of its teaching staff, and an innovative learning method aimed at educating the professionals of the future”
A revolutionary study method, a cutting-edge faculty and a practical focus: the key to TECH's success.
The most complete study plans on the university scene
TECH offers the most complete study plans on the university scene, with syllabuses that cover fundamental concepts and, at the same time, the main scientific advances in their specific scientific areas. In addition, these programs are continuously being updated to guarantee students the academic vanguard and the most in-demand professional skills. In this way, the university's qualifications provide its graduates with a significant advantage to propel their careers to success.
TECH offers the most comprehensive and intensive study plans on the current university scene.
A world-class teaching staff
TECH's teaching staff is made up of more than 6,000 professors with the highest international recognition. Professors, researchers and top executives of multinational companies, including Isaiah Covington, performance coach of the Boston Celtics; Magda Romanska, principal investigator at Harvard MetaLAB; Ignacio Wistumba, chairman of the department of translational molecular pathology at MD Anderson Cancer Center; and D.W. Pine, creative director of TIME magazine, among others.
Internationally renowned experts, specialized in different branches of Health, Technology, Communication and Business, form part of the TECH faculty.
A unique learning method
TECH is the first university to use Relearning in all its programs. It is the best online learning methodology, accredited with international teaching quality certifications, provided by prestigious educational agencies. In addition, this disruptive educational model is complemented with the “Case Method”, thereby setting up a unique online teaching strategy. Innovative teaching resources are also implemented, including detailed videos, infographics and interactive summaries.
TECH combines Relearning and the Case Method in all its university programs to guarantee excellent theoretical and practical learning, studying whenever and wherever you want.
The world's largest online university
TECH is the world’s largest online university. We are the largest educational institution, with the best and widest online educational catalog, one hundred percent online and covering the vast majority of areas of knowledge. We offer a large selection of our own degrees and accredited online undergraduate and postgraduate degrees. In total, more than 14,000 university degrees, in eleven different languages, make us the largest educational largest in the world.
TECH has the world's most extensive catalog of academic and official programs, available in more than 11 languages.
Google Premier Partner
The American technology giant has awarded TECH the Google Google Premier Partner badge. This award, which is only available to 3% of the world's companies, highlights the efficient, flexible and tailored experience that this university provides to students. The recognition as a Google Premier Partner not only accredits the maximum rigor, performance and investment in TECH's digital infrastructures, but also places this university as one of the world's leading technology companies.
Google has positioned TECH in the top 3% of the world's most important technology companies by awarding it its Google Premier Partner badge.
The official online university of the NBA
TECH is the official online university of the NBA. Thanks to our agreement with the biggest league in basketball, we offer our students exclusive university programs, as well as a wide variety of educational resources focused on the business of the league and other areas of the sports industry. Each program is made up of a uniquely designed syllabus and features exceptional guest hosts: professionals with a distinguished sports background who will offer their expertise on the most relevant topics.
TECH has been selected by the NBA, the world's top basketball league, as its official online university.
The top-rated university by its students
Students have positioned TECH as the world's top-rated university on the main review websites, with a highest rating of 4.9 out of 5, obtained from more than 1,000 reviews. These results consolidate TECH as the benchmark university institution at an international level, reflecting the excellence and positive impact of its educational model.” reflecting the excellence and positive impact of its educational model.”
TECH is the world’s top-rated university by its students.
Leaders in employability
TECH has managed to become the leading university in employability. 99% of its students obtain jobs in the academic field they have studied, within one year of completing any of the university's programs. A similar number achieve immediate career enhancement. All this thanks to a study methodology that bases its effectiveness on the acquisition of practical skills, which are absolutely necessary for professional development.
99% of TECH graduates find a job within a year of completing their studies.
Postgraduate Diploma in Industrial Robotics
Are you looking for a way into the exciting world of factory engineering and robots? Are you passionate about technology and would like to become an expert in this ever-growing field? If so, our Industrial Robotics Postgraduate Diploma program is perfect for you! Industrial robotics is a fascinating discipline that combines engineering, programming and innovation to develop smart and efficient solutions for industrial production. With the increasing demand for automation in industries, there is an urgent need for highly trained professionals in this area. Our postgraduate program will provide you with all the knowledge and skills you need to enter this exciting field. Through a practical online and project-based approach, you will immerse yourself in the study of different types of industrial robots, their design and operation, as well as their programming.
Get certified online and advance professionally
During the program, you will be supported by highly qualified teachers with extensive experience in the robotics industry. In addition, you will have access to the latest technologies and tools used in the field, allowing you to acquire up-to-date and relevant training. One of the main advantages of our program is its flexibility. You will be able to study at your own pace, adapting your schedule according to your daily needs and commitments. This will allow you to combine your studies with other responsibilities and make the most of your time. At the end of your studies, you will receive a Postgraduate Diploma in Industrial Robotics, endorsed by our prestigious academic institution. This certificate will open the doors to a wide range of job opportunities in companies in the industrial and technological sector. Seize the opportunity and take the first step towards a successful career in the exciting field of industrial robotics - enroll in our Industrial Robotics Postgraduate Diploma program today and become an expert in the technology of the future!