University certificate
The world's largest school of business”
Why study at TECH?
Improve the efficiency and quality of your company's production processes thanks to this Professional master’s degree in Lean Manufacturing"
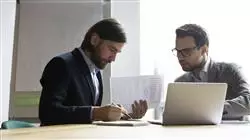
Why Study at TECH?
TECH is the world's largest 100% online business school. It is an elite business school, with a model based on the highest academic standards. A world-class center for intensive managerial skills education.
TECH is a university at the forefront of technology, and puts all its resources at the student's disposal to help them achieve entrepreneurial success"
At TECH Global University
|
Innovation |
The university offers an online learning model that combines the latest educational technology with the most rigorous teaching methods. A unique method with the highest international recognition that will provide students with the keys to develop in a rapidly-evolving world, where innovation must be every entrepreneur’s focus.
"Microsoft Europe Success Story", for integrating the innovative, interactive multi-video system.
|
The Highest Standards |
Admissions criteria at TECH are not economic. Students don't need to make a large investment to study at this university. However, in order to obtain a qualification from TECH, the student's intelligence and ability will be tested to their limits. The institution's academic standards are exceptionally high...
95% of TECH students successfully complete their studies.
|
Networking |
Professionals from countries all over the world attend TECH, allowing students to establish a large network of contacts that may prove useful to them in the future.
100,000+ executives trained each year, 200+ different nationalities.
|
Empowerment |
Students will grow hand in hand with the best companies and highly regarded and influential professionals. TECH has developed strategic partnerships and a valuable network of contacts with major economic players in 7 continents.
500+ collaborative agreements with leading companies.
|
Talent |
This program is a unique initiative to allow students to showcase their talent in the business world. An opportunity that will allow them to voice their concerns and share their business vision.
After completing this program, TECH helps students show the world their talent.
|
Multicultural Context |
While studying at TECH, students will enjoy a unique experience. Study in a multicultural context. In a program with a global vision, through which students can learn about the operating methods in different parts of the world, and gather the latest information that best adapts to their business idea.
TECH students represent more than 200 different nationalities.
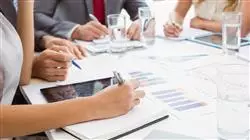
|
Learn with the best |
In the classroom, TECH teaching staff discuss how they have achieved success in their companies, working in a real, lively, and dynamic context. Teachers who are fully committed to offering a quality specialization that will allow students to advance in their career and stand out in the business world.
Teachers representing 20 different nationalities.
TECH strives for excellence and, to this end, boasts a series of characteristics that make this university unique:
|
Analysis |
TECH explores the student’s critical side, their ability to question things, their problem-solving skills, as well as their interpersonal skills.
|
Academic Excellence |
TECHoffers students the best online learning methodology. The university combines the Relearning method (a postgraduate learning methodology with the highest international rating) with the Case Study. A complex balance between tradition and state-of-the-art, within the context of the most demanding academic itinerary.
|
Economy of Scale |
TECH is the world’s largest online university. It currently boasts a portfolio of more than 10,000 university postgraduate programs. And in today's new economy, volume + technology = a ground-breaking price. This way, TECH ensures that studying is not as expensive for students as it would be at another university.
At TECH, you will have access to the most rigorous and up-to-date case studies in the academic community”
Syllabus
This Professional master’s degree in Lean Manufacturing has been designed to provide students with 1,500 hours of first-level education in this field. A learning program of great practical and direct use in their organizations so that they can improve at the same time as the students who take this program. All this, in addition, with a pedagogical approach in line with the current times and the real needs of professionals in the industrial and business sector.
The video clips will support this process of updating knowledge on project management, leadership and problem solving"
Syllabus
The syllabus of this academic option has been designed to provide students with a rigorous and exhaustive knowledge of the Lean Manufacturing methodology and its integration in organizations.
A teaching that will lead the graduate throughout this academic itinerary to carry out a deep analysis of this management philosophy, its principles, the implementation of strategies to achieve the proposed results. All this, in addition, complemented by video summaries of each topic, videos in detail, specialized readings and case studies easily accessible through a digital device with internet connection and at any time of the day.
In this way, you will learn in a much more dynamic way about the difference between processes and flow, value stream mapping, flow generation, quality management and continuous improvement or Total Productive Maintenance TPM.
Likewise, with the Relearning system, based on the continuous reiteration of key concepts, the professional will not have to invest long hours of study and memorization, since this method focuses on the most important concepts, thus making it much easier to consolidate them.
This is a great opportunity for students seeking a complete and intensive learning experience through a flexible academic option that adapts to the daily schedule of the graduate and his or her motivations for professional progression in a business environment that requires qualified personnel with a high level of management knowledge.
This Professional master’s degree takes place over 12 months and is divided into 10 modules:
Module 1. Lean Manufacturing Principles and Context
Module 2. Value and Waste (Duration): Identification and elimination of non-value-adding activities
Module 3. Value Stream Mapping: Analysis and Mapping of the flow of materials, information and activities in a process. Flow optimization
Module 4. Continuous Flow: Process design for smooth and continuous workflows
Module 5. Pull system: implementation of a demand-driven production system to control production and minimize inventory
Module 6. Lean Quality Management
Module 7. Continuous improvement, Kaizen
Module 8. Evolution of production organization in a Lean system
Module 9. TPM (Total Productive Maintenance), OEE (Overall Equipment Effectiveness)
Module 10. Lean implementation: Strategies and best practices for implementing Lean Manufacturing in an organization
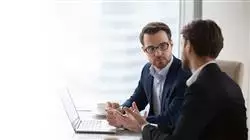
Where, When and How is it Taught?
TECH offers the possibility of doing this Professional master’s degree in Lean Manufacturing completely online. Throughout the 12 months of the educational program, you will be able to access all the contents of this program at any time, allowing you to self-manage your study time.
Module 1. Lean Manufacturing Principles and Context
1.1. Lean Manufacturing
1.1.1. Lean Manufacturing. Origin
1.1.2. Lean Manufacturing Principles
1.1.3. Benefits of Lean Manufacturing Methodology
1.2. Benefits of Lean Manufacturing Methodology Production philosophy at the Toyota plant
1.2.1. Toyota Production System (TPS)
1.2.2. Key principles of the TPS
1.2.3. The Pillars of TPS
1.3. Precursors of Lean Manufacturing
1.3.1. Kiichiro Toyoda, Taiichi Ohno and Shigeo Shingo
1.3.2. Edward Deming
1.3.3. James Womack, Daniel Jones and Michael George
1.4. Lean Concept and its Application in Production
1.4.1. Value Identification and Value Stream Mapping
1.4.2. Creation of continuous flow and establishment of Pull Production
1.4.3. Pursuit of Perfection
1.5. Lean Manufacturing y Gestión de la Calidad Total
1.5.1. Lean Manufacturing y Total Quality Management
1.5.2. Commonalities between Lean Manufacturing and Total Quality Management
1.5.3. Differences between Lean Manufacturing and Total Quality Management
1.6. Lean Manufacturing y 6 Sigma
1.6.1. Lean Manufacturing y 6 Sigma
1.6.2. Commonalities between Lean Manufacturing and 6 Sigma
1.6.3. Differences between Lean Manufacturing and 6 Sigma
1.7. Lean Manufacturing and Process Reengineering
1.7.1. Lean Manufacturing and Process Reengineering
1.7.2. Commonalities between Lean Manufacturing and process reengineering
1.7.3. Differences between Lean Manufacturing and Process Reengineering
1.8. Lean Manufacturing y Teoría de las limitaciones (TOC)
1.8.1. Lean Manufacturing y Teoría de las limitaciones (TOC)
1.8.2. Commonalities between Lean Manufacturing and Theory of Constraints (TOC)
1.8.3. Differences between Lean Manufacturing Theory of Constraints (TOC)
1.9. Lean Manufacturing. Integration with Industry 4.0
1.9.1. Evolution of Lean Manufacturing in the Industry 4.0 era.
1.9.2. Integration of Lean Manufacturing with Industry 4.0
1.9.3. Future of Lean Manufacturing in the era of Industry 4.0
1.10. Applications of the Lean philosophy in other areas: Lean Logistics, Lean Office, Lean Service
1.10.1. Lean Logistics, Lean Office, Lean Service. Applications
1.10.2. Lean Logistics applications
1.10.3. Lean Office applications
1.10.4. Lean Service
Module 2. Value and Waste (Duration): Identification and elimination of non-value-added activities
2.1. Concept of "Value" from the Customer's Perspective
2.1.1. Satisfaction of customer needs
2.1.2. Perceived value vs. Tangible value
2.1.3. Value for money
2.2. Quality Function Deployment
2.2.1. Quality Function Deployment. Concept and Definition
2.2.2. Techniques for identifying customer needs
2.2.3. Quality deployment
2.3. Mura in Lean Manufacturing
2.3.1. Demand Variability
2.3.2. Production Variability
2.3.3. Supply Variability
2.4. Muri in Lean Manufacturing
2.4.1. Equipment overload
2.4.2. Overloading people
2.4.3. System overload
2.5. Mudas related to Manufacturing
2.5.1. Overproduction
2.5.2. Types and Causes of Overproduction
2.5.3. Unnecessary processing
2.6. Quality-related mutations
2.6.1. Quality Defects for rework or scrap
2.6.2. Causes of Quality Defects
2.6.3. Scrap vs. rework
2.7. Transportation related mutations
2.7.1. Unnecessary Transportation
2.7.2. Causes of Waiting Times
2.7.3. Strategies to avoid/minimize waiting times
2.8. Excess Inventory-related debts
2.8.1. Excess inventories of PM
2.8.2. Excess of in-process inventories
2.8.3. Excess inventories of finished product
2.9. Mudas related to the waiting/social times
2.9.1. Types of waiting time
2.9.2. Causes of waiting times
2.9.3. Strategies to avoid/minimize waiting times
2.10. New Mudas defined
2.10.1. Lack of Staff Training
2.10.2. Poor utilization of Staff Skills and Abilities
2.10.3. Resources dedicated to non-strategic or priority processes
Module 3. Value stream mapping: Analysis and Mapping of the flow of materials, information and activities in a process. Flow optimization
3.1. The Value Stream Map. Value Stream Mapping.(VSM)
3.1.1. Value stream
3.1.2. The value stream map
3.1.3. Selection of a product family
3.2. Connection, Strategy and tactics with the VSM
3.2.1. The Quality Cost Delivery (QCD). The customer is in charge
3.2.2. Hoshin Kanri, from vision to tactics
3.2.3. Visual Management as a mechanism for prioritization and alignment
3.3. Value Stream Map in current status
3.3.1. Value stream mapping
3.3.2. Symbols used in the design of the Value Stream Map
3.3.3. Data Collection
3.4. The timing of a value stream map VSM
3.4.1. Takt Time, the rhythm set by the customer
3.4.2. Cycle Time
3.4.3. Lead Time, the necessary end-to-end time
3.5. The Lean value chain
3.5.1. Problem of overproduction
3.5.2. Characteristics of a Lean value chain
3.5.3. Creation of continuous flow to create Lean processes
3.6. Future State Value Stream Map
3.6.1. Value stream mapping
3.6.2. Symbols used for future design
3.6.3. From the future map to the work plan
3.7. Value chain planning and improvement
3.7.1. Implementation planning
3.7.2. Prioritization of activities
3.7.3. Connecting VSM to strategy
3.8. Value Supply Chain Management
3.8.1. Mapping of the current state of the Supply Chain
3.8.2. Symbols used for its design
3.8.3. Design of the future supply chain
3.9. Value Stream Project Management, the Lean Project
3.9.1. Peculiarities of a Project vs. a Process
3.9.2. The value stream of a project
3.9.3. Analysis of the current state and design of the future
3.10. Yokoten
3.10.1. Yokoten. Fundamentals
3.10.2. The 3 phases of Yokoten
3.10.3. Standard Solution Cycle
Module 4. Continuous flow: Process Design for smooth and continuous workflows
4.1. Continuous Flow
4.1.1. Flow Creation in the Toyota Production System
4.1.2. The Fourteen Principles of the Toyota Way Culture
4.1.3. Total Flow Management, the union of Flow Creation and Pull Flow System
4.2. Processes
4.2.1. Typology of industrial processes
4.2.2. Apartments vs. Processes vs. Flows
4.2.3. Process integration
4.3. Flows
4.3.1. The different types of flows: Materials, Equipment, People and Information
4.3.2. Job-shop vs. Flow-shop
4.3.3. Turbulent flows vs. Linear flows
4.4. Machines, Equipment and Lines
4.4.1. Hardware Reliability as an Essential Element for Flow Creation
4.4.2. Jidoka philosophy as an essential element in Flow Creation
4.4.3. Monument machine vs. Lean Machine
4.5. Materials
4.5.1. Traditional plant layout vs. Lean plant layout
4.5.2. PFEP (Plan-For-Each-Part)
4.5.3. Batch production vs. One-piece-flow (Continuous flow)
4.6. Person
4.6.1. The Internal Customer, concept in a lean environment
4.6.2. The role of a lean manager
4.6.3. The role of a lean operator
4.7. Information
4.7.1. Enterprise Resource Planning System (ERP)
4.7.2. Information systems specific to the industrial environment
4.7.3. Dashboard, as part of the Daily Management System
4.8. Lean Flow System
4.8.1. Muda expulsion in the production process
4.8.2. The Autonomous Cell as a lean paradigm
4.8.3. Lean support tools: 5S, Visual Management, SMED
4.9. Flow Creation application examples
4.9.1. Example of implementation in the automotive sector
4.9.2. Example of application in the metallurgical sector
4.9.3. Example of use in the food sector
4.10. Creation of Flow: Design, Implementation and Improvement of Production Processes. Practical Application
4.10.1. Design for flow creation
4.10.2. Implementation of continuous flow
4.10.3. Improvement of production processes
Module 5. Pull system: implementation of a demand-driven production system to control production and minimize inventory
5.1. Pull System. Fundamentals
5.1.1. Pull Flow System: the fourth principle of Lean Thinking
5.1.2. Push vs. Pull processes
5.1.3. Stability, Flexibility, Synchronization, Concentration
5.2. Demand.
5.2.1. Types of demand
5.2.2. Takt Time, Production Time, Lead Time
5.2.3. Production + Logistics Contract
5.3. Flows
5.3.1. End-to-End: from suppliers to customers
5.3.2. Logistics + Production Connection
5.3.3. Supply routes
5.4. Machines, Equipment and Lines
5.4.1. Logistics train
5.4.2. Containers
5.4.3. Shelving
5.5. Materials
5.5.1. Warehouses
5.5.2. Supermarkets
5.5.3. Line edge
5.6. Person
5.6.1. Pull Flow system managers
5.6.2. Logistics and production operators
5.6.3. The “Mizusumashi” (“Water spider”)
5.7. Information
5.7.1. Heijunka (Leveling): Leveling box + Logistics box
5.7.2. Kanban
5.7.3. Batch Conformer + Sequencer
5.8. Lean Pull Flow System
5.8.1. Balanced
5.8.2. On-line sequencing
5.8.3. Lean support tools: VSM, OEE, Standard Work, One-point-lesson, Andon
5.9. Examples of Pull Flow System applications
5.9.1. Example of implementation in the automotive sector
5.9.2. Example of application in the metallurgical sector
5.9.3. Example of use in the food sector
5.10. Pull system: Design, Implementation and Improvement of Production Processes. Practical Application
5.10.1. Design of a pull system
5.10.2. Implementation of the pull flow system
5.10.3. Improvement of information in production processes
Module 6. Lean quality management
6.1. Quality Management in Lean Manufacturing
6.1.1. Quality defined as customer satisfaction
6.1.2. Production quality: consistency and conformity
6.1.3. Specifications and quality costs
6.2. Quality measurement: quality indicators
6.2.1. Definition of indicators
6.2.2. Construction of indicators
6.2.3. Examples of a quality scorecard
6.3. Quality systems and lean quality vision
6.3.1. Quality systems and regulations
6.3.2. Compatibility of ISO - TS with Lean Manufacturing
6.3.3. Compatibility of EFQM and Lean Manufacturing
6.4. Concept of "Genchi Genbutsu" (Gemba) and Quality Management. Relevance
6.4.1. Concept of "Genchi Genbutsu" (Gemba)
6.4.2. Application of the concept in practice. Example in the automotive sector
6.4.3. Application of the concept in practice. Example from the capital goods sector
6.5. Standardization and Simplification in quality management using "Standard Work".
6.5.1. Standard Work. Concept and benefits
6.5.2. Application of Standard Work in industry
6.5.3. Example of the application of Standard Work in a process
6.6. The Jidoka philosophy for early detection of quality problems
6.6.1. Detection of quality problems at source
6.6.2. Production line stoppage
6.6.3. Examples of the application of the Jidoka philosophy in industry
6.7. Andon as a tool for Quality Management
6.7.1. Definition, origin and benefits of Andon
6.7.2. Andon types and examples
6.7.3. Implementation of the Andon system
6.8. "Poka-Yoke. Quality Technology
6.8.1. PokaYoke. Types and causes of errors that prevent
6.8.2. Poka-yoke design process
6.8.3. Examples of Poka- Yoke
6.9. Visual Management
6.9.1. Process visualization
6.9.2. Visual signage
6.9.3. Visual records
6.10. Lean and IOT quality management and Blockchain
6.10.1. Benefits of combining IoT and lean quality management
6.10.1.1. Sensorization for process monitoring
6.10.1.2. Real-time traceability systems and data analytics for quality management
6.10.2. Benefits of combining Lean and Blockchain in quality management.
6.10.2.1. Application of smart contracts for quality assurance and regulatory compliance
6.10.2.2. Design and implementation of a secure and scalable Blockchain infrastructure for quality management.
Module 7. Continuous improvement, Kaizen
7.1. Continuous Improvement and Kaizen in Lean Manufacturing
7.1.1. Continuous improvement and Kaizen
7.1.2. The PDCA/PDSA cycle. Comparison of problem solving methods
7.1.3. Encouraging the participation of the entire organization in kaizen.
7.2. Implementation of the PDCA/PDSA cycle
7.2.1. Plan
7.2.2. Do
7.2.3. Check/Study
7.2.4. Act
7.2.5. Application Examples
7.3. Implementation of "6M" to identify opportunities for improvement
7.3.1. Method Analysis
7.3.2. Machine Analysis
7.3.3. Materials Analysis
7.3.4. Measurement system analysis
7.3.5. Analysis of the external environment
7.3.6. Analysis of the problems generated by People?
7.4. Statistical Methods of Process Control
7.4.1. Process control and statistical methods in process control
7.4.2. Statistics for process control
7.4.3. Common statistical methods in process control
7.5. Causal Analysis: Data Science
7.5.1. Ishikawa Diagram
7.5.2. 5 reasons
7.5.3. Other techniques for root cause analysis
7.6. Application of the 5 S's in continuous improvement
7.6.1. Seiri (Classification): Elimination of unnecessary elements
7.6.2. Seiton (Order): Workplace organization
7.6.3. Seiso (Cleaning): Maintaining a clean and orderly work environment
7.6.4. Seiketsu (Standardization): Establishment of standards and procedures
7.6.5. Shitsuke (Discipline): Maintenance of standards and continuous improvement
7.7. Continuous improvement and IoT
7.7.1. Real-time data collection for process analysis
7.7.2. Process automation to reduce variability and improve quality
7.7.3. Efficiency improvement and cost reduction through remote process monitoring
7.8. Sustaining the Kaizen culture in the long term
7.8.1. Long-term commitment of senior management
7.8.2. Integration of Kaizen as part of the company's culture and not as an add-on/accessory.
7.8.3. Measuring results and long-term incentives for improvements, adapting them to the organizational context
7.9. Practical examples of continuous improvement in different industries
7.9.1. Example in the automotive industry
7.9.2. Example in the food industry
7.9.3. Example in the construction supply industry
7.10. Future trends in continuous improvement
7.10.1. Development of digital tools and platforms for continuous improvement
7.10.2. Incorporation of new project management approaches: User-centered design and evidence-based development
7.10.3. Incorporating emotional intelligence in continuous improvement
Module 8. Evolution of production organization in a Lean system
8.1. The organization of production in a Lean system
8.1.1. The Organization of Production. Key Concepts
8.1.2. Company Structure and Organization
8.1.3. Production systems and work organization
8.2. Organizational differences between a traditional production system and a Lean system
8.2.1. Types of organizational structure
8.2.2. Organizational differences between a traditional system and a Lean system
8.2.3. Organizational advantages of the Lean system
8.3. Concept of "Work Cells" and their impact on efficiency and continuous improvement
8.3.1. Advantages of "Work Cells".
8.3.2. Structure/ Types of "Work Cells".
8.3.3. Management routines "Work Cells" to impact efficiency and continuous improvement
8.4. Implementation of "Continuous Improvement Teams" (Kaizen Teams) to ensure a focus on continuous improvement and problem solving
8.4.1. Incorporation of the Kaizen Teams Concept in the organization.
8.4.2. Activities and methodology
8.4.3. Kaizen Teams Roles and Responsibilities
8.5. Importance of "Autonomy and Accountability" in the evolution towards a lean system and the improvement of efficiency and quality.
8.5.1. Self-managed and agile teams as a key to organizational evolution
8.5.2. The development of people as an added value to the Lean organization.
8.5.3. Structure for leading "Autonomy and accountability" towards a Lean system
8.6. Use of Standard Work to standardize processes and encourage continuous improvement
8.6.1. Standard Work. Key Elements
8.6.2. Benefits of Standard Work as an object of continuous improvement
8.6.3. Implementation of Standard Work in organizations
8.7. Systems for promoting polyvalence and training in lean organizations: The polyvalence matrix
8.7.1. Polyvalence Promotion and Training Systems in Lean Organizations: The Polyvalence Matrix
8.7.2. Advantages of a multipurpose system
8.7.3. Implementation of the polyvalence promotion system
8.8. Evolution of production organization through waste elimination and continuous improvement
8.8.1. Analysis of non-value-adding activities as a basic Lean practice
8.8.2. Waste elimination/reduction strategy
8.8.3. Implementing a waste elimination/reduction model
8.9. Implementation of Work Cells and continuous improvement groups in different industries. Practical Examples
8.9.1. Implementation of Work Cells in the Automotive Sector
8.9.2. Implementation of work cells in the textile sector.
8.9.3. Implementation of Work Cells in the Food Sector
8.10. Importance of the evolution of the production organization towards a Lean system.
8.10.1. Main aspects in the evolution towards a Lean system
8.10.2. Improved productivity and production organization
8.10.3. Utility of the Lean System for the evolution of the production organization.
Module 9. TPM (Total Productive Maintenance), OEE (Overall Equipment Effectiveness)
9.1. TPM Total Productive Maintenance
9.1.1. TPM Total Productive Maintenance. Fundamentals
9.1.2. Emergence, objectives and benefits
9.1.3. TPM Pillars
9.2. Improved machine efficiency OEE: Problem Identification and Problem Solving Techniques
9.2.1. Identification of efficiency problems
9.2.2. Solving efficiency problems
9.2.3. Machine efficiency monitoring
9.3. Techniques to Reduce Downtime in the Production Process, Maintenance Planning and Programming
9.3.1. Production planning and maintenance
9.3.2. Autonomous Maintenance
9.3.3. SMED
9.4. Equipment Maintenance Management and Purchasing. Decision Criteria
9.4.1. Technical requirements and specifications
9.4.2. Costs and investment
9.4.3. Supplier evaluation: criteria
9.5. Preventative Maintenance Prevention of equipment failures
9.5.1. Installation of the equipment: Maintainability criteria
9.5.2. Preventative Maintenance
9.5.3. Example of a preventive maintenance plan in the railway industry
9.6. Predictive Maintenance Equipment failure prediction
9.6.1. Predictive Maintenance
9.6.2. Sensorization of equipment
9.6.3. Algorithm development with AI
9.7. Safety Improvement Techniques in the Production Process, Identification and Elimination of Hazards in the Workplace
9.7.1. Identification of hazards in the workplace
9.7.2. Risk assessment and protection measures
9.7.3. Emergency Planning
9.8. Guidance for the Implementation of TPM in the Organization, Planning, Training and Implementation of Maintenance Systems
9.8.1. The 14 steps for TPM implementation
9.8.2. Implementation planning
9.8.3. TPM training and maintenance
9.9. Improved energy efficiency: How to optimize energy use and reduce costs through the implementation of TPM
9.9.1. Energy efficiency of equipment
9.9.2. Measuring consumption and efficiency
9.9.3. Identification and elimination of energy losses and improvement
9.10. Examples of TPM implementation
9.10.1. Example of application in the railway sector
9.10.2. Examples in the pharmaceutical sector
9.10.3. Example of application in the sector
Module 10. Lean implementation: Strategies and best practices for implementing Lean Manufacturing in an organization.
10.1. Lean implementation. Project Start
10.1.1. Vision and reasons for change
10.1.2. Definition of the action framework and objectives
10.1.3. Selection of the initial project team
10.1.4. Definition of the Project Charter
10.2. Analysis of the current state of the company's processes: Evaluation and identification of areas for improvement and opportunities when implementing the Lean philosophy.
10.2.1. Identification of key processes
10.2.2. Analysis of the current state of the organization and processes.
10.2.3. Technical Analysis/Current culture and main management systems
10.3. Selection of a multidisciplinary work team to lead the Lean philosophy implementation project in the company.
10.3.1. Identification of necessary skills and competencies
10.3.2. Selection of persons
10.3.3. Formation of the Kaizen Teams
10.4. Definition and establishment of clear and measurable objectives for the implementation of the Lean philosophy in the company.
10.4.1. Definition of indicators
10.4.2. Measurement of Indicators
10.4.3. Definition of goals to be achieved at different horizons
10.5. Planning and development of the project to implement the Lean philosophy in the company. Allocation of resources and execution deadlines
10.5.1. Scope Definition
10.5.2. Definition of actions to be carried out and resources required
10.5.3. Definition of the calendar
10.6. Formation of the work team: Training in Lean methodology for the selected work team and other company employees.
10.6.1. Assessment of the knowledge/capabilities of the implementation team
10.6.2. Design of the training plan
10.6.3. Development of the training plan
10.7. Selection of the Pilots to be developed at the beginning
10.7.1. Criteria for selection of pilot scopes
10.7.2. Criteria for selection of persons to be involved who do not belong to the promoter's team
10.7.3. Initial evaluation before starting the pilots
10.8. Development and Implementation of Pilots and Quick Wins
10.8.1. Development of a detailed plan to implement Lean in the selected pilot processes.
10.8.2. Implementation of Quick Wins. Quick Wins Identification and Execution: Improvements to be implemented in the short term in the pilot processes
10.8.3. Continuous monitoring and adjustment of pilots to measure results and make adjustments as needed
10.9. Establishment of global performance indicators: Definition of indicators and key performance indicators (KPIs) to measure the success of the implementation of the Lean philosophy.
10.9.1. Definition of medium and long term SMART objectives
10.9.2. Definition of key indicators to be followed
10.9.3. Follow-up and communication of progress
10.10. Development of a plan to extend the Lean philosophy to the rest of the organization.
10.10.1. Identification of extension areas: criteria
10.10.2. Establishment of the extension plan: pace and resources
10.10.3. Project implementation, monitoring and communication
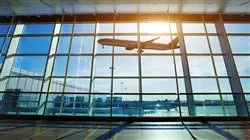
Incorporate the most up-to-date effectiveness measurement and evaluation tools into your project and differentiate yourself in your sector".
Professional Master's Degree in Lean Manufacturing
Modern industry is facing increasingly fierce competition and, as a result, efficiency and productivity are key factors in business success. In order to compete in this environment, it is essential to have highly trained professionals in the field of production. That is why TECH Global University offers the Professional Master's Degree in Lean Manufacturing, a high-level training that will allow you to develop your skills and competencies in the field of production and management. In the Professional Master's Degree in Lean Manufacturing taught by the prestigious TECH Business School, you will find the necessary tools to improve production efficiency and increase product quality, thus achieving greater competitiveness. In addition, this online class program will allow you to study at your own pace, from anywhere and at any time, with the possibility of adapting the learning to your needs and schedules.
Study Lean Manufacturing and improve your production skills.
The methodology of this Professional Master's Degree in Lean Manufacturing is based on the Lean philosophy, which seeks to reduce production times and minimize costs, without compromising the quality of products or services. In this postgraduate course, we will provide you with a complete preparation in this approach, and we will teach you how to apply it in your company so that you can achieve the best results. In addition, you will have a team of highly qualified professors with extensive experience in the field of production and business management. If you want to improve your production skills and become an expert in Lean Manufacturing, do not hesitate to enroll in the Professional Master's Degree at TECH, the best digital university in the world. This academic proposal will open the doors to new job opportunities, as companies are looking for professionals capable of improving the efficiency and productivity of their processes.