University certificate
The world's largest school of business”
Why study at TECH?
Industrial companies demand managers with extensive experience, but, above all, with a strategic and international vision of the business that will help them achieve success"Â
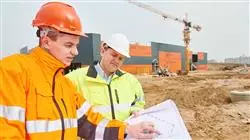
Why Study at TECH?
TECH is the world's largest 100% online business school. It is an elite business school, with a model based on the highest academic standards. A world-class centre for intensive managerial skills training.  Â
TECH is a university at the forefront of technology, and puts all its resources at the student's disposal to help them achieve entrepreneurial success"
At TECH Global University
|
Innovation |
The university offers an online learning model that combines the latest educational technology with the most rigorous teaching methods. A unique method with the highest international recognition that will provide students with the keys to develop in a rapidly-evolving world, where innovation must be every entrepreneur’s focus.
"Microsoft Europe Success Story", for integrating the innovative, interactive multi-video system. Â
|
The Highest Standards |
Admissions criteria at TECH are not economic. Students don't need to make a large investment to study at this university. However, in order to obtain a qualification from TECH, the student's intelligence and ability will be tested to their limits. The institution's academic standards are exceptionally high... Â
95% of TECH students successfully complete their studies.
|
Networking |
Professionals from countries all over the world attend TECH, allowing students to establish a large network of contacts that may prove useful to them in the future. Â
+100.000 executives trained each year, 200+ different nationalities.
|
Empowerment |
Students will grow hand in hand with the best companies and highly regarded and influential professionals. TECH has developed strategic partnerships and a valuable network of contacts with major economic players in 7 continents. Â
+500 collaborative agreements with leading companies.
|
Talent |
This program is a unique initiative to allow students to showcase their talent in the business world. An opportunity that will allow them to voice their concerns and share their business vision.Â
After completing this program, TECH helps students show the world their talent.Â
|
Multicultural Context |
While studying at TECH, students will enjoy a unique experience. By studying in a multicultural context. In a program with a global vision, through which students can learn about the operating methods in different parts of the world, and gather the latest information that best adapts to their business idea.Â
TECH students represent more than 200 different nationalities.  Â

|
Learn with the best |
In the classroom, TECH teaching staff discuss how they have achieved success in their companies, working in a real, lively, and dynamic context. Teachers who are fully committed to offering a quality specialization that will allow students to advance in their career and stand out in the business world.Â
Teachers representing 20 different nationalities.Â
TECH strives for excellence and, to this end, boasts a series of characteristics that make this university unique:  Â
|
Analysis |
TECH explores the student’s critical side, their ability to question things, their problem-solving skills, as well as their interpersonal skills. Â
|
Academic Excellence |
TECH offers students the best online learning methodology. The university combines the Re-learning methodology (the most internationally recognized postgraduate learning methodology) with Harvard Business School case studies. A complex balance of traditional and state-of-the-art methods, within the most demanding academic framework.  Â
|
Economy of Scale |
TECH is the world’s largest online university. It currently boasts a portfolio of more than 10,000 university postgraduate programs. And in today's new economy, volume + technology = a ground-breaking price. This way, TECH ensures that studying is not as expensive for students as it would be at another university. Â
At TECH you will have access to Harvard Business School case studies"  
Syllabus
The Advanced master’s degree in Senior Management in Industrial Companies is a program designed to enable business professionals to specialize in a field that is increasingly in demand. A program that is taught in 100% online format and that will be indispensable for the development of students, who will find in it the best content of the current academic panorama on the management of industrial companies. And, all of this, with the most innovative didactic methodology on the market.Â
A very well-structured syllabus in a fully digital format that will allow you to self-manage your study time" Â
Syllabus
The Advanced master’s degree in Senior Management in Industrial Companies from TECH Global University is an intensive program that prepares the professional to face business challenges and decisions at both national and international levels. Its content is designed to promote the development of managerial skills that enable more rigorous decision-making in uncertain environments.Â
Throughout 3,000 hours of study, the student will analyze a multitude of practical cases through individual work, achieving high quality learning that can be applied to their daily practice. It is, therefore, an authentic immersion in real business situations. Â
This program deals in depth with the main areas of the company and is designed for managers to understand the management of industrial projects from a strategic, international and innovative perspective.Â
A plan designed for students, focused on their professional improvement and preparing them to achieve excellence in the field of industrial management. A program that understands both yours and your company's needs through innovative content based on the latest trends, and supported by the best educational methodology and an exceptional faculty, which will provide you with the skills to solve critical situations, creatively and efficiently.Â
This Advanced master’s degree takes place over 2 years and is divided into 20 modules:Â
Module 1. Strategic Keys to Improve Competitiveness
Module 2. Project Management
Module 3. Leadership and People Management
Module 4. Corporate Finance An Economic-Financial Approach
Module 5. Design and Product Development
Module 6. Production Planning and Control
Module 7. Lean Manufacturing
Module 8. Quality Management
Module 9. The Logistics Function, Key to Compete
Module 10. Industry 4.0 and Business Intelligence The Digitized Company
Module 11. International Projects
Module 12. Turnkey Projects (EPC)
Module 13. Management and Control of Stages in Turnkey Projects (EPC)
Module 14. Contract Management in Projects
Module 15. Risk Management in Contract Management
Module 16. Project Management in Contract Management
Module 17. Project Management in Projects: Scope and Schedule Management
Module 18. Project Management in Projects: Communications and Quality Management
Module 19. Project Management in Projects: Procurement and Resource ManagementÂ
Module 20. Project Management in Projects: Cost Management
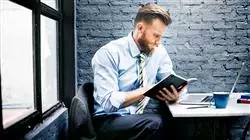
Where, When and How is it Taught?
TECH offers the possibility of taking this program completely online. Throughout the 2 years of training, the student will be able to access all the contents of this program at any time, allowing them to self-manage their study time.Â
Module 1. Strategic Keys to Improve Competitiveness Â
1.1. Excellence in the Current CompanyÂ
1.1.1. Adaptation to VUCA EnvironmentsÂ
1.1.2. Satisfaction of Key Constituents (Stakeholders)Â
1.1.3. World Class ManufacturingÂ
1.1.4. Measure of Excellence: Net Promoter ScoreÂ
1.2. Business Strategy DesignÂ
1.2.1. General Strategy Definition ProcessÂ
1.2.2. Definition of the Current Situation Positioning ModelsÂ
1.2.3. Possible Strategic MovementsÂ
1.2.4. Strategic Models of ActionÂ
1.2.5. Functional and Organizational StrategiesÂ
1.2.6. Environmental and Organizational Analysis SWOT Analysis for Decision-MakingÂ
1.3. Strategy Deployment Balanced ScorecardÂ
1.3.1. Mission, Vision, Values and PrinciplesÂ
1.3.2. Need for a Balanced ScorecardÂ
1.3.3. Perspectives to Be Used in the BSCÂ
1.3.4. Strategic MapÂ
1.3.5. Phase to Implement a Good BSCÂ
1.3.6. General Map of a BSC
1.4. Process ManagementÂ
1.4.1. Process DescriptionÂ
1.4.2. Types of Process Main ProcessesÂ
1.4.3. Process PrioritizationÂ
1.4.4. Process RepresentationÂ
1.4.5. Measuring Processes for ImprovementÂ
1.4.6. Process MapÂ
1.4.7. Process ReengineeringÂ
1.5. Structural Typologies Agile Organizations. ERRÂ
1.5.1. Structural Typologies
1.5.2. The Company Seen as an Adaptable SystemÂ
1.5.3. The Horizontal CompanyÂ
1.5.4. Characteristics and Key Factors of Agile Organizations (ERR)Â
1.5.5. Organizations of the Future: the TEAL OrganizationÂ
1.6. Design of Business ModelsÂ
1.6.1. CANVAS Model for Business Model DesignÂ
1.6.2. Lean Start-up Methodology in the Creation of New Businesses and ProductsÂ
1.6.3. The Blue Ocean StrategyÂ
1.7. Corporate Social Responsibility and SustainabilityÂ
1.7.1. Corporate Social Responsibility (CSR): ISO Business School 26000Â
1.7.2. Sustainable Development Goals SDGsÂ
1.7.3. The 2030 AgendaÂ
1.8. Customer ManagementÂ
1.8.1. The Need to Manage Customer RelationshipsÂ
1.8.2. Elements of Customer Management Â
1.8.3. Technology and Customer Management. CRMÂ
1.9. Management in International EnvironmentsÂ
1.9.1. The Importance of the InternationalisationÂ
1.9.2. Diagnosis of Export PotentialÂ
1.9.3. Elaboration of the Internationalisation PlanÂ
1.9.4. Implementation of the Internationalization PlanÂ
1.9.5. Export Assistance ToolsÂ
1.10. Change ManagementÂ
1.10.1. The Dynamics of Change in CompaniesÂ
1.10.2. Obstacles to ChangeÂ
1.10.3. Factors of Adaptation to ChangeÂ
1.10.4. Kotter's Methodology for Change ManagementÂ
Module 2. Project Management
2.1. The ProjectÂ
2.1.1. Fundamental Elements of the ProjectÂ
2.1.2. The Project ManagerÂ
2.1.3. The Environment in Which Projects OperateÂ
2.2. Project Scope ManagementÂ
2.2.1. Scope AnalysisÂ
2.2.2. Project Scope PlanningÂ
2.2.3. Project Scope ControlÂ
2.3. Schedule ManagementÂ
2.3.1. The Importance of the PlanningÂ
2.3.2. Manage Project Planning Project Schedule
2.3.3. Trends in Time ManagementÂ
2.4. Cost ManagementÂ
2.4.1. Project Cost AnalysisÂ
2.4.2. Financial Selection of ProjectsÂ
2.4.3. Project Cost PlanningÂ
2.4.4. Project Cost ControlÂ
2.5. Quality, Resources and AcquisitionsÂ
2.5.1. Total Quality and Project ManagementÂ
2.5.2. Project ResourcesÂ
2.5.3. Acquisition The Contracting SystemÂ
2.6. Project Stakeholders and Their CommunicationsÂ
2.6.1. The Importance of StakeholdersÂ
2.6.2. Project Stakeholder ManagementÂ
2.6.3. Project CommunicationsÂ
2.7. Project Risk ManagementÂ
2.7.1. Fundamental Principles of Risk ManagementÂ
2.7.2. Management Processes for Project Risk ManagementÂ
2.7.3. Trends in Risk ManagementÂ
2.8. Integrated Project ManagementÂ
2.8.1. Strategic Planning and Project ManagementÂ
2.8.2. Project Management PlanÂ
2.8.3. Execution and Control ProcessesÂ
2.8.4. Project ClosureÂ
2.9. Agile Methodologies I: ScrumÂ
2.9.1. Agile and Scrum PrinciplesÂ
2.9.2. The ScrumTeamÂ
2.9.3. Scrum EventsÂ
2.9.4. Scrum ArtefactsÂ
2.10. Agile Methodologies II: KanbanÂ
2.10.1. Kanban PrinciplesÂ
2.10.2. Kanban and ScrumbanÂ
2.10.3. CertificationsÂ
Module 3. Leadership and People Management Â
3.1. The Role of the LeaderÂ
3.1.1. Leadership in Effective People ManagementÂ
3.1.2. Types of Decision-Making Style in People ManagementÂ
3.1.3. The Leader CoachÂ
3.1.4. Self-Directed Teams and EmpowermentÂ
3.2. Team MotivationÂ
3.2.1. Needs and ExpectationsÂ
3.2.2. Effective RecognitionÂ
3.2.3. How to Enhance Team CohesionÂ
3.3. Communication and Conflict ResolutionÂ
3.3.1. Intelligent CommunicationÂ
3.3.2. Constructive Conflict Management Â
3.3.3. Conflict Resolution StrategiesÂ
3.4. Emotional Intelligence in People ManagementÂ
3.4.1. Emotion, Feeling and State of MindÂ
3.4.2. Emotional IntelligenceÂ
3.4.3. Ability Model (Mayer and Salovey): Identify, Use, Understand and ManageÂ
3.4.4. Emotional Intelligence and Personnel SelectionÂ
3.5. Indicators in People ManagementÂ
3.5.1. ProductivityÂ
3.5.2. Personnel RotationÂ
3.5.3. Talent Retention RateÂ
3.5.4. Staff Satisfaction RateÂ
3.5.5. Average Time Vacancies Pending FillingÂ
3.5.6. Average Training TimeÂ
3.5.7. Average Time to Reach GoalsÂ
3.5.8. Absenteeism LevelsÂ
3.5.9. Occupational AccidentsÂ
3.6. Performance EvaluationÂ
3.6.1. Performance Evaluation Components and CycleÂ
3.6.2. 360º EvaluationÂ
3.6.3. Performance Management: A Process and a SystemÂ
3.6.4. Management by ObjectivesÂ
3.6.5. Operation of the Performance Evaluation ProcessÂ
3.7. Training PlanÂ
3.7.1. Fundamental PrinciplesÂ
3.7.2. Identification of Training RequirementsÂ
3.7.3. Training PlanÂ
3.7.4. Training and Development IndicatorsÂ
3.8. Identification of PotentialÂ
3.8.1. PotentialÂ
3.8.2. Soft Skills as a Key High Potential InitiatorÂ
3.8.3. Methodologies for Identifying Potential: Learning Agility Assessment (Lominger) and Growth FactorsÂ
3.9. The Talent MapÂ
3.9.1. George Odiorne-4 Boxes MatrixÂ
3.9.2. 9-Box MatrixÂ
3.9.3. Strategic Actions to Achieve Effective Talent Outcomes
3.10. Talent Development Strategy and ROIÂ
3.10.1. 70-20-10 Learning Model for Soft SkillsÂ
3.10.2. Career Paths and SuccessionÂ
3.10.3. Talent ROIÂ
Module 4. Corporate Finance And Economic-Financial Approach Â
4.1. The Company in Our EnvironmentÂ
4.1.1. Production CostsÂ
4.1.2. Companies in Competitive MarketsÂ
4.1.3. Monopolistic CompetitionÂ
4.2. Analysis of Financial Statements I: The BalanceÂ
4.2.1. The Assets CP and LP ResourcesÂ
4.2.2. Liabilities CP and LP ObligationsÂ
4.2.3. Net Assets Shareholder ReturnsÂ
4.3. Analysis of Financial Statements II: the Income StatementÂ
4.3.1. The Structure of the Income Statement Income, Costs, Expenses and Profit or Loss
4.3.2. Main Ratios to Analyze the Income Statement
4.3.3. Profitability AnalysisÂ
4.4. Treasury ManagementÂ
4.4.1. Collections and Payments Cash-ForecastÂ
4.4.2. Impact and Management of Treasury Deficits/Surplus Corrective Measures
4.4.3. Effect Flows Analysis
4.4.4. Bad Debt Portfolio Management and ImpactÂ
4.5. Sources of Financing to CP and LPÂ
4.5.1. CP Financing, InstrumentsÂ
4.5.2. LP Financing, InstrumentsÂ
4.5.3. Types of Interest and Their StructureÂ
4.6. Interaction between the Company and the BankÂ
4.6.1. The Financial System and the Banking BusinessÂ
4.6.2. Corporate Banking ProductsÂ
4.6.3. The Company Analyzed by the BankÂ
4.7. Analytical or Cost AccountingÂ
4.7.1. Cost Types Decisions Based on Costs
4.7.2. Full-CostingÂ
4.7.3. Direct CostingÂ
4.7.4. Cost Model by Center and by ActivityÂ
4.8. Investment Analysis and ValuationÂ
4.8.1. The Company and the Investment Decisions Scenarios and Situations Â
4.8.2. Investment ValuationÂ
4.8.3. Company ValuationÂ
4.9. Corporate AccountingÂ
4.9.1. Capital Increase and Reduction Â
4.9.2. Dissolution, Liquidation and Transformation of CompaniesÂ
4.9.3. Combination of Companies: Mergers and AcquisitionsÂ
4.10. Foreign Trade FinanceÂ
4.10.1. Foreign Markets: The Decision to ExportÂ
4.10.2. The Foreign Exchange MarketÂ
4.10.3. International Payment and Collection MethodsÂ
4.10.4. Transportation, Incoterms and InsuranceÂ
Module 5. Design and Product Development Â
5.1. QFD in Product Design and Development (Quality Function Deployment)Â
5.1.1. From the Voice of the Customer to Technical RequirementsÂ
5.1.2. The House of Quality/Phases for its DevelopmentÂ
5.1.3. Advantages and LimitationsÂ
5.2. Design ThinkingÂ
5.2.1. Design, Need, Technology and StrategyÂ
5.2.2. Process StagesÂ
5.2.3. Used Tools and TechniquesÂ
5.3. Concurrent Engineering
5.3.1. Concurrent Engineering FundamentalsÂ
5.3.2. Concurrent Engineering MethodologiesÂ
5.3.3. Used ToolsÂ
5.4. Program. Planning and DefinitionÂ
5.4.1. Requirements. Quality ManagementÂ
5.4.2. Development Phases Time ManagementÂ
5.4.3. Materials, Feasibility, Processes Cost ManagementÂ
5.4.4. Project Team Human Resource ManagementÂ
5.4.5. Information. Communication ManagementÂ
5.4.6. Risk Analysis Risk Management
5.5. Product. Design (CAD) and DevelopmentÂ
5.5.1. Information Management/PLM/Product Life CycleÂ
5.5.2. Product Failure Modes and EffectsÂ
5.5.3. CAD Construction ReviewsÂ
5.5.4. Product and Manufacturing DrawingsÂ
5.5.5. Design VerificationÂ
5.6. Prototypes. Development Â
5.6.1. Rapid PrototypingÂ
5.6.2. Control PlanÂ
5.6.3. Experiment DesignÂ
5.6.4. Analysis of Measuring SystemsÂ
5.7. Productive Process. Design and Development Â
5.7.1. Modes and Effects of Process FailureÂ
5.7.2. Design and Construction of Manufacturing ToolingÂ
5.7.3. Design and Construction of Checking Fixtures (Gauges)Â
5.7.4. Adjustment PhasesÂ
5.7.5. Production Start-UpÂ
5.7.6. Initial Process EvaluationÂ
5.8. Product and Process. ValidationÂ
5.8.1. Evaluation of Measurement SystemsÂ
5.8.2. Validation TestsÂ
5.8.3. Statistical Process Control (SPC)Â
5.8.4. Product Certification Â
5.9. Change Management. Improvement and Corrective Actions Â
5.9.1. Types of changeÂ
5.9.2. Variability Analysis, ImprovementÂ
5.9.3. Lessons Learned and Proven PracticesÂ
5.9.4. Process of Change Â
5.10. Innovation and Technology TransferÂ
5.10.1. Intellectual PropertyÂ
5.10.2. InnovationÂ
5.10.3. Technology TransferÂ
Module 6. Production Planning and Control Â
6.1. Phases of Production PlanningÂ
6.1.1. Advanced PlanningÂ
6.1.2. Sales Forecasting, MethodsÂ
6.1.3. Takt-Time DefinitionÂ
6.1.4. Material Plan-MRP-Minimum Stock Â
6.1.5. Personnel PlanÂ
6.1.6. Equipment NeedsÂ
6.2. Production Plan (PDP)Â
6.2.1. Factors to ConsiderÂ
6.2.2. Push PlanningÂ
6.2.3. Pull PlanningÂ
6.2.4. Mixed SystemsÂ
6.3. KanbanÂ
6.3.1. Types of KanbanÂ
6.3.2. Kanban UsesÂ
6.3.3. Autonomous Planning: 2-Bin KanbanÂ
6.4. Production ControlÂ
6.4.1. PDP Deviations and ReportingÂ
6.4.2. Production Performance Monitoring: OEEÂ
6.4.3. Total Capacity Tracking: TEEPÂ
6.5. Production OrganizationÂ
6.5.1. Production TeamÂ
6.5.2. Process EngineeringÂ
6.5.3. MaintenanceÂ
6.5.4. Material ControlÂ
6.6. Total Productive Maintenance (TPM)Â
6.6.1. Corrective MaintenanceÂ
6.6.2. Autonomous MaintenanceÂ
6.6.3. Preventative MaintenanceÂ
6.6.4. Predictive MaintenanceÂ
6.6.5. Maintenance Efficiency Indicators MTBF - MTTR
6.7. Plant LayoutÂ
6.7.1. Conditioning FactorsÂ
6.7.2. In-Line ProductionÂ
6.7.3. Production in Work CellsÂ
6.7.4. ApplicationsÂ
6.7.5. SLP MethodologyÂ
6.8. Just-In-Time (JIT)Â
6.8.1. Description and Origins of JITÂ
6.8.2. ObjectivesÂ
6.8.3. Application of JIT Product Sequencing  Â
6.9. Theory of Constraints (TOC)Â
6.9.1. Fundamental PrinciplesÂ
6.9.2. The 5 Steps of TOC and Its ApplicationÂ
6.9.3. Advantages and DisadvantagesÂ
6.10. Quick Response Manufacturing (QRM)Â
6.10.1. DescriptionÂ
6.10.2. Key Points for StructuringÂ
6.10.3. QRM ImplementationÂ
Module 7. Lean Manufacturing
7.1. Lean ThinkingÂ
7.1.1. Structure of the Lean SystemÂ
7.1.2. Lean PrinciplesÂ
7.1.3. Lean Versus Traditional Manufacturing Processes
7.2. Waste in the CompanyÂ
7.2.1. Value Vs. Waste in Lean EnvironmentsÂ
7.2.2. Types of Waste (MUDAS)Â
7.2.3. Lean Process of ThinkingÂ
7.3. The 5 SÂ
7.3.1. 5S Principles and How They Can Help Improve ProductivityÂ
7.3.2. The 5 S: Seiri, Seiton, Seiso, Seiketsu and ShitsukeÂ
7.3.3. Implementation of the 5 S in the CompanyÂ
7.4. Lean Diagnostic Tools. VSM. Value Stream MapsÂ
7.4.1. Value Adding Activities (VA), Necessary Activities (NNVA) and Non-Value Adding Activities (NVA)Â
7.4.2. The 7 Tools of Value Stream mapping(Value Stream Mapping)Â
7.4.3. Process Activity MappingÂ
7.4.4. Supply Chain Response MappingÂ
7.4.5. The Production Variety FunnelÂ
7.4.6. Quality Filter MappingÂ
7.4.7. Demand Amplification MappingÂ
7.4.8. Decision Point AnalysisÂ
7.4.9. Mapping of the Physical StructureÂ
7.5. Lean Operational ToolsÂ
7.5.1. SmedÂ
7.5.2. JidokaÂ
7.5.3. Poka-YokeÂ
7.5.4. Batch ReductionÂ
7.5.5. Pous Poka-YokeÂ
7.6. Lean Tools for Production Monitoring, Planning and Control Â
7.6.1. Visual ManagementÂ
7.6.2. StandardizationÂ
7.6.3. Production Leveling (Heijunka)Â
7.6.4. Cellular ManufacturingÂ
7.7. The Kaizen Method for Continuous ImprovementÂ
7.7.1. Kaizen Principles Â
7.7.2. Kaizen Methodologies Kaizen Blitz, Gemba Kaizen, Kaizen TeianÂ
7.7.3. Problem Solving Tools A3 Report, Â
7.7.4. Main Obstacles to Kaizen ImplementationÂ
7.8. Roadmap for Lean ImplementationÂ
7.8.1. General Aspects of ImplementationÂ
7.8.2. Phases of ImplementationÂ
7.8.3. Information Technologies in Lean ImplementationÂ
7.8.4. Success Factors in Lean ImplementationÂ
7.9. KPIs for Measuring Lean Performance Â
7.9.1. OEE- Overall Equipment EfficiencyÂ
7.9.2. TEEP- Total Effective Equipment Effectiveness PerformanceÂ
7.9.3. FTT- First-Time QualityÂ
7.9.4. DTD- Dock to Dock TimeÂ
7.9.5. OTD- On-Time DeliveryÂ
7.9.6. BTS- Manufacturing According to ProgramÂ
7.9.7. ITO- Inventory Turnover RateÂ
7.9.8. VAR- Value Added RatioÂ
7.9.9. PPMs- Parts Per Million DefectsÂ
7.9.10. FR- Delivery Fulfillment RateÂ
7.9.11. IFA-Accident Frequency IndexÂ
7.10. The Human Dimension of Lean. Staff Participation SystemsÂ
7.10.1. The Lean Project Team Application of TeamworkÂ
7.10.2. Operator VersatilityÂ
7.10.3. Improvement GroupsÂ
7.10.4. Suggestion ProgramsÂ
Module 8. Quality Management Â
8.1. Total QualityÂ
8.1.1. Total Quality ManagementÂ
8.1.2. External and Internal CustomerÂ
8.1.3. Quality CostsÂ
8.1.4. Continuous Improvement and the Deming PhilosophyÂ
8.2. ISO 9001:15 Quality Management SystemÂ
8.2.1. The 7 Principles of ISO 9001:15 Quality Management Â
8.2.2. The Process ApproachÂ
8.2.3. ISO 9001:15 RequirementsÂ
8.2.4. Stages and Recommendations for ImplementationÂ
8.2.5. Deployment Objectives in a Hoshin-Kanri-type Model Â
8.2.6. Certification AuditÂ
8.3. Integrated Management Systems
8.3.1. Environmental Management System ISO Business School 14000Â
8.3.2. Occupational Risk Management System: ISO Business School 45001Â
8.3.3. Integration of Management SystemsÂ
8.4. Excellence in Management: EFQM ModelÂ
8.4.1. Principles and Fundamentals of EFQM ModelÂ
8.4.2. New Criteria of the EFQM ModelÂ
8.4.3. EFQM Diagnostic Tool: REDER MatrixesÂ
8.5. Quality ToolsÂ
8.5.1. Basic ToolsÂ
8.5.2. SPC Statistical Process ControlÂ
8.5.3. Control Plan and Control Guidelines for Product Quality ManagementÂ
8.6. Advanced Tools and Troubleshooting ToolsÂ
8.6.1. FMEAÂ
8.6.2. 8D ReportÂ
8.6.3. The 5 WhysÂ
8.6.4. The 5W + 2HÂ
8.6.5. BenchmarkingÂ
8.7. Continuous Improvement Methodology I: PDCAÂ
8.7.1. The PDCA Cycle and Its StagesÂ
8.7.2. Application of the PDCA Cycle to Lean Manufacturing DevelopmentÂ
8.7.3. Keys to Success of PDCA ProjectsÂ
8.8. Continuous Improvement Methodology II: Six-SigmaÂ
8.8.1. Six-Sigma DescriptionÂ
8.8.2. Six-Sigma PrinciplesÂ
8.8.3. Six-Sigma Project SelectionÂ
8.8.4. Six-Sigma Project Stages DMAIC MethodologyÂ
8.8.5. Six-Sigma RolesÂ
8.8.6. Six-Sigma and Lean ManufacturingÂ
8.9. Quality Suppliers. Audits. Testing and LaboratoryÂ
8.9.1. Reception Quality Concerted QualityÂ
8.9.2. Internal Audits Management SystemÂ
8.9.3. Product and Process Audits Â
8.9.4. Phases to Perform AuditsÂ
8.9.5. Auditor ProfileÂ
8.9.6. Testing, Laboratory and MetrologyÂ
8.10. Organizational Aspects of Quality ManagementÂ
8.10.1. Management's Role in Quality ManagementÂ
8.10.2. Organization of the Quality Area and the Relationship with Other AreasÂ
8.10.3. Quality CirclesÂ
Module 9. The Logistics Function, Key to Compete
9.1. Logistical Function of and the Supply ChainÂ
9.1.1. Logistics Is the Key to a Company's SuccessÂ
9.1.2. Logistics ChallengesÂ
9.1.3. Key Activities to Logistics How to Obtain Logistic Function ValueÂ
9.1.4. Types of Supply ChainÂ
9.1.5. Supply Chain ManagementÂ
9.1.6. Logistics CostsÂ
9.2. Logistics Optimization StrategiesÂ
9.2.1. Cross-Docking StrategyÂ
9.2.2. Application of Agile Methodology to Logistics ManagementÂ
9.2.3. Outsourcing of Logistic ProcessesÂ
9.2.4. Picking or Efficient Order PickingÂ
9.3. Lean LogisticsÂ
9.3.1. Lean Logistics in Supply Chain ManagementÂ
9.3.2. Analysis of Waste in the Logistics ChainÂ
9.3.3. Application of a Lean System in Supply Chain ManagementÂ
9.4. Warehouse Management and AutomationÂ
9.4.1. The Role of WarehousesÂ
9.4.2. Warehouse ManagementÂ
9.4.3. Stocks ManagementÂ
9.4.4. Warehouse TypologyÂ
9.4.5. Load UnitsÂ
9.4.6. Organization of a WarehouseÂ
9.4.7. Storage and Handling Elements
9.5. Procurement ManagementÂ
9.5.1. The Role of Distribution as an Essential Part of Logistics. Internal Vs. External LogisticsÂ
9.5.2. The Traditional Relationship with SuppliersÂ
9.5.3. The New Paradigm of Supplier RelationshipsÂ
9.5.4. How to Classify and Select New SuppliersÂ
9.5.5. How to Develop Effective Procurement ManagementÂ
9.6. Information Systems and Logistics ControlÂ
9.6.1. Requirements of a Logistics Information and Control SystemÂ
9.6.2. 2 Types of Information Systems and Logistics ControlÂ
9.6.3. Big Data Applications in Logistics ManagementÂ
9.6.4. The Importance of Data in Logistics ManagementÂ
9.6.5. The Balanced Scorecard Applied to Logistics Main Management and Control Indicators
9.7. Reverse LogisticsÂ
9.7.1. Keys to Reverse LogisticsÂ
9.7.2. Reverse Vs. Direct Logistics FlowsÂ
9.7.3. Operations within the Framework of Reverse LogisticsÂ
9.7.4. How to Implement a Reverse Distribution ChannelÂ
9.7.5. Final Alternatives for Products in the Reverse ChannelÂ
9.7.6. Costs of Reverse LogisticsÂ
9.8. New Logistic StrategiesÂ
9.8.1. Artificial Intelligence and RobotizationÂ
9.8.2. Green Logistics and SustainabilityÂ
9.8.3. Internet of Things Applied to LogisticsÂ
9.8.4. The Digitized WarehouseÂ
9.8.5. E-businessand the New Distribution ModelsÂ
9.8.6. The Importance of Last Mile Logistics
9.9. Retail Chain Benchmarking Â
9.9.1. Commonalities of Successful Value ChainsÂ
9.9.2. Inditex Group Value Chain AnalysisÂ
9.9.3. Amazon Value Chain AnalysisÂ
9.10. Pandemic LogisticsÂ
9.10.1. General ScenarioÂ
9.10.2. Critical Supply Chain Issues in a Pandemic ScenarioÂ
9.10.3. Implications of Cold Chain Requirements on the Establishment of the Vaccine Supply ChainÂ
9.10.4. Types of Supply Chains for the Distribution of VaccinesÂ
Module 10. Industry 4.0 and Business Intelligence. The Digitized Company Â
10.1. Automation and Industrial RoboticsÂ
10.1.1. Phases in Process AutomationÂ
10.1.2. Industrial Hardware for Automation and RoboticsÂ
10.1.3. The Work Cycle and Its Programming SoftwareÂ
10.2. Process Automation: RPAÂ
10.2.1. Automatable Administrative ProcessesÂ
10.2.2. Software StructureÂ
10.2.3. Examples of ApplicationÂ
10.3. MES, SCADA, GMAO, SGA, MRPII Systems
10.3.1. Product Control with MES Systems Â
10.3.2. Engineering and Maintenance SCADA and GMAOÂ
10.3.3. Procurement and Logistics: SGA and MPRII
10.4. Business Intelligence SoftwareÂ
10.4.1. Fundamentals of BIÂ
10.4.2. Software StructureÂ
10.4.3. Application PossibilitiesÂ
10.5. ERP SoftwareÂ
10.5.1. ERP DescriptionÂ
10.5.2. Use ReachÂ
10.5.3. Leading ERPs in the MarketÂ
10.6. IoT and Business IntelligenceÂ
10.6.1. IoT: the Connected WorldÂ
10.6.2. Data SourcesÂ
10.6.3. Total Control through IoT + BIÂ
10.6.4. BlockchainÂ
10.7. Main BI Software in the MarketÂ
10.7.1. Power BIÂ
10.7.2. QlikÂ
10.7.3. TableauÂ
10.8. Microsoft Power BIÂ
10.8.1. FeaturesÂ
10.8.2. Examples of ApplicationÂ
10.8.3. The Future of Power BIÂ
10.9. Machine Learning, Artificial Intelligence, Optimization and Prediction in the EnterpriseÂ
10.9.1. Machine Learning and Artificial IntelligenceÂ
10.9.2. Process OptimizationÂ
10.9.3. The Importance of Data Driven Forecasting Â
10.10. Big Data Applied to the Business EnvironmentÂ
10.10.1. Applications in the Production EnvironmentÂ
10.10.2. Applications at the Strategic Management LevelÂ
10.10.3. Applications in Marketing and SalesÂ
Module 11. International ProjectsÂ
11.1. Projects and Organizational Context
11.1.1. Projects in the Organisation
11.1.2. Project Elements
11.1.3. The Importance of the Project in the Organisation
11.2. Types of Projects by Service
11.2.1. Types of Projects
11.2.2. Project Analysis
11.2.3. Project Orientation
11.3. Main Processes in the Development of a ProjectÂ
11.3.1. Start-up and Planning Process
11.3.2. Execution and Monitoring
11.3.3. Closing Process
11.4. Cost, Scope and Quality Constraints AnalysisÂ
11.4.1. Cost Restriction Analysis
11.4.2. Scope Restriction
11.4.3. Quality Restriction
11.5. Time, Resource and Risk Restrictions
11.5.1. Time Restriction Analysis
11.5.2. Resource Restrictions
11.5.3. Risk Restrictions
11.6. Analysis of Contract TypesÂ
11.6.1. Unit Price ContractÂ
11.6.2. Lump Sum Contract
11.6.3. Cost Plus Margin Contract
11.7. Project Management by TypologyÂ
11.7.1. Project Management at Unit Price
11.7.2. Lump Sum Project Management
11.7.3. Cost Plus Margin Project Management
11.8. Project, Program and Portfolio
11.8.1. Analysis of the Project in the Organisation
11.8.2. Analysis of the Program in the Organization
11.8.3. Analysis of the Portfolio in the Organization
11.9. Stakeholders in the Project
11.9.1. Project Stakeholder Pyramid
11.9.2. Analysis of the Stakeholders
11.9.3. Interaction of the Stakeholders
11.10. Analysis of the Organization's Process Assets
11.10.1. Asset Analysis in Start-up and Planning
11.10.2. Analysis of Assets in Execution and Control
11.10.3. Analysis of Assets at Closing
Module 12. Turnkey Projects (EPC)Â
12.1. EPC Project
12.1.1. EPC Project Context
12.1.2. Project Components
12.1.3. Needs Analysis
12.2. EPC Project Stages
12.2.1. Identification of Stages in EPC Projects
12.2.2. Identification of Initial Needs in Stages
12.2.3. Timing of Each Stage
12.3. Management of the E-Engineering Stage Â
12.3.1. Analysis of Stage E
12.3.2. Timeline for Stage E
12.3.3. Necessary Resources for Stage E
12.4. Analysis of the E-Engineering StageÂ
12.4.1. Structure Required for Stage E Development
12.4.2. Restrictions
12.4.3. Difficulties and Risks
12.5. Management of the P-Procurement StageÂ
12.5.1. Analysis of Stage P
12.5.2. Timeline
12.5.3. Resources Required
12.6. Analysis of the P-Procurement StageÂ
12.6.1. Structure Required for Stage P Development
12.6.2. Restrictions
12.6.3. Difficulties and Risks
12.7. Management of the C-Construction StageÂ
12.7.1. Analysis of Stage C
12.7.2. Timeline
12.7.3. Resources Required
12.8. Analysis of the C-Construction StageÂ
12.8.1. Structure Required for Stage C Development
12.8.2. Restrictions
12.8.3. Difficulties and Risks
12.9. EPC Projects: HR DepartmentÂ
12.9.1. Main Functions
12.9.2. Resources Required for This Department
12.9.3. Coordination and Communications with the Rest of the Project
12.10. EPC Projects: Contracts Department
12.10.1. Main Functions
12.10.2. Resources Required for This Department
12.10.3. Coordination and Communications with the Rest of the Project
Module 13. Management and Control of Stages in Turnkey Projects (EPC)Â
13.1. Coordination of Stages in EPC Projects
13.1.1. Stage Planning
13.1.2. Communications between Teams
13.1.3. Incident Resolution of Process Stages
13.2. Stage C: Main Structural Components: Quality
13.2.1. Component Q Quality
13.2.2. Analysis of the Quality Part of the Project
13.2.3. Structure and Importance
13.3. Stage C: Main Structural Components: Health and Safety
13.3.1. HSE Component Health and Safety
13.3.2. Analysis of the Health and Safety Part of the Project
13.3.3. Structure and Importance
13.4. Stage C: Main Structural Components: Costs
13.4.1. Component C. Cost
13.4.2. Analysis of the Cost Control Part of the Project
13.4.3. Structure and Importance
13.5. Stage C: Main Structural Components: Deadline
13.5.1. Component P. Time FrameÂ
13.5.2. Analysis of the Deadline Control Part of the Project
13.5.3. Structure and Importance
13.6. International EPC Project ManagementÂ
13.6.1. Project Manager Management
13.6.2. Characteristics of the Manager
13.6.3. Coordination and Communication
13.7. International EPC Project AnalysisÂ
13.7.1. Global Analysis of the Project from the Management
13.7.2. Management Reporting Processes
13.7.3. Control of the Main KPIs of the Project
13.8. EPC Project Deviations
13.8.1. Main EPC Project DeviationsÂ
13.8.2. Deviations Analysis
13.8.3. Customer Deviation Notifications Procedure
13.9. Analysis and Monitoring of Economic Deviations of the Project with Respect to Contract
13.9.1. Production Control
13.9.2. Cost Control
13.9.3. Product Monitoring Vs. Cost
13.10. Non-conformity Management in EPC Projects
13.10.1. Main Non-conformities in EPC Projects
13.10.2. Management Procedures
13.10.3. Analysis and Mitigation
Module 14. Contract Management in Projects
14.1. Contract Management in Projects
14.1.1. Contract Management Analysis in Projects
14.1.2. Need for Contract Management
14.1.3. Contract Management Objectives
14.2. Functions of Contract ManagerÂ
14.2.1. Main Functions of the CM in Projects
14.2.2. Characteristics of the CM Position
14.2.3. Contract Management Indicators
14.3. Contract Management Process
14.3.1. Design of a Contract Management Plan
14.3.2. Management Plan Stages
14.3.3. Contract Management Adversities
14.4. Contract Management Success Factors
14.4.1. Analysis of Main Success Factors
14.4.2. Planning and Development of Contract Management
14.4.3. Performance Management and Partner Relationships
14.5. Main Stage of Contract Management
14.5.1. Planning and Execution
14.5.2. Control and Monitoring During Execution
14.5.3. Control and Monitoring After Execution
14.6. Factors to Take into Account in the Management of Construction Contracts
14.6.1. Setting Objectives and Strategies
14.6.2. Design and Construction Phase of Lump SumContracts
14.6.3. Relations with Contractors
14.7. Contract Manager Challenges
14.7.1. Successful Contract Management and Administration
14.7.2. Customer Communications Management
14.7.3. Contract Analysis and Performance
14.8. Aspects to Resolve
14.8.1. Contract Negotiation and Approval
14.8.2. Control During Ejection
14.8.3. Control of Compliance with Contractual Obligations
14.9. Aspects to Be Supervised
14.9.1. Contract Negotiation and Approval
14.9.2. Control During Ejection
14.9.3. Control of Compliance with Contractual Obligations
14.10. Management of Project Factors by the Contract Manager
14.10.1. Scope Management
14.10.2. Cost ManagementÂ
14.10.3. Risk and Change Management
Module 15. Risk Management in Contract Management
15.1. International Contract Management Â
15.1.1. Contract Management According to PMBOOKÂ
15.1.2. Procurement Control and Management According to PMBOOK
15.1.3. Importance and Involvement of the Contract Manager
15.2. Contract Management & Project Management
15.2.1. Relationship betweenContract Management & Project Management
15.2.2. Collaboration between CM and PM
15.2.3. Control of Major Construction Site Factors
15.3. Risk Management by Contract ManagerÂ
15.3.1. Identification of Contract Risks
15.3.2. Risk Classification
15.3.3. Matrix Development and Implementation
15.4. Risk Analysis by Contract ManagerÂ
15.4.1. Identification of Risk Managers
15.4.2. Follow-up of Evolution
15.4.3. Risk Mitigation
15.5. Types of Guarantees
15.5.1. Classification
15.5.2. Importance of Collateral Management
15.5.3. Costs and Expiration
15.6. Penalty Analysis
15.6.1. Type of Penalties According to Contract
15.6.2. Penalty Control by the Contract Manager
15.6.3. Effective Contract Managementt in the Face of Penalties
15.7. Construction Insurance Management
15.7.1. Types of Construction Insurance
15.7.2. Insurance Deadlines
15.7.3. Importance of Insurance
15.8. Analysis of Construction Insurance
15.8.1. Contract Management in Insurance Management
15.8.2. Calculations and Costs for Construction Insurance
15.8.3. Validity of Insurance
15.9. Contract Management and Legal Department
15.9.1. Conexion of the Contract Manager and Legal Department
15.9.2. Importance of Legal Knowledge of the Contract manager
15.9.3. Communication from the Legal Point of View of the Contract manager
15.10. Contract Manager and Contractors
15.10.1. Contract manager Communications with the Contractor
15.10.2. Follow-up of the Contract with the Contractor
15.10.3. Importance of Communications Traceability Control
Module 16. Project Management in Contract Management
16.1. Contract Managementand Budget
16.1.1. Objectives of Budget Management by the Contract Manager
16.1.2. Main Types of Budgets
16.1.3. Budget According to Cost Structure
16.2. Contract Management and Site Control
16.2.1. Objectives of Site Control Management
16.2.2. Hiring of an Inspection Body
16.2.3. Verification and Monitoring of the Work
16.3. Contract Management and Health and Safety Control on Site
16.3.1. Objectives of Health and Safety Control Management at the Construction Site
16.3.2. Aspects to Consider for Health and Safety control
16.3.3. On-site Verification and Follow-up
16.4. Contract Managementand Subcontracting
16.4.1. Importance of the Contract Manager 's Involvement in the Management of Subcontracting Contracts
16.4.2. Types of Subcontracting Contracts
16.4.3. Analysis of Contracts with Subcontractors
16.5. Subcontracting Process to Be Followed by the Contract Manager
16.5.1. Bidding and Comparison
16.5.2. Pre-selection and Pre-recruitment
16.5.3. Subcontract Award
16.6. Monitoring of Changes in Subcontractor Contracts
16.6.1. Importance of Change Tracking
16.6.2. Control of Changes in Time and Cost
16.6.3. Need for Timely Notifications
16.7. Contract Management and Outsourcing Contract
16.7.1. Basics of the Outsourcing Services Contract
16.7.2. Contract Managementin This Type of Contracts
16.7.3. Points to Consider
16.8. Contract Management and Contract Disputes
16.8.1. Intervention of the Contract Manager in Disputes
16.8.2. Technical and Legal Difficulty in International Arbitration Cases
16.8.3. Importance of the Contract Management in Future Disputes
16.9. Classification of Disputes and Arbitrations
16.9.1. Types of Disputes and Arbitrations
16.9.2. Preparing Documentation for Disputes
16.9.3. Importance of Traceability in Future Disputes
16.10. Customers: Manager and Customer
16.10.1. Customers: manager Communications with the Customer
16.10.2. Follow-up of the Contract with the Customer
16.10.3. Importance of Communications Traceability Control
Module 17. Project Management in Projects: Scope and Schedule Management
17.1. Scope Control
17.1.1. Scope of the Project
17.1.2. Project Scope Baseline
17.1.3. The Importance of the Control Account
17.2. Requirement Management
17.2.1. Requirements Management
17.2.2. Categories
17.2.3. Management Process
17.3. Scope ManagementÂ
17.3.1. Planning and Scope Management
17.3.2. Gather Requirements
17.3.3. Particularities of Scope
17.4. Scope AnalysisÂ
17.4.1. Preparation of the WBS
17.4.2. Scope Validation
17.4.3. Scope Control
17.5. Timeline Control
17.5.1. Project Timeline
17.5.2. Baseline of the Timeline
17.5.3. Critical Path Analysis
17.6. Timeline Elaboration
17.6.1. Gantt Chart
17.6.2. Predecessor and Successor Activities
17.6.3. Restrictions between Activities
17.7. Schedule ManagementÂ
17.7.1. Planning and Timeline Management
17.7.2. Activity Description
17.7.3. Activity Sequencing
17.8. Study and Analysis of the TimelineÂ
17.8.1. Estimated Duration of Activities
17.8.2. Development of the Timeline
17.8.3. Timeline Control
17.9. Construction Project Acceleration Plan
17.9.1. Analysis of the Acceleration Plan
17.9.2. Timeline
17.9.3. Resources
17.10. Recovery Plan in Construction Project
17.10.1. Analysis of the Recuperation Plan
17.10.2. Timeline
17.10.3. Resources
Module 18. Project Management in Projects: Communications and Quality Management
18.1. Communication Control
18.1.1. Project CommunicationsÂ
18.1.2. Dimensions of Project CommunicationÂ
18.1.3. Communication Skills
18.2. Project Communications
18.2.1. Communication in Meetings
18.2.2. Channels of Project Communication
18.2.3. Formal Ways of Communication
18.3. Communication Management
18.3.1. Planning of Communication Management
18.3.2. Project Communications Management
18.3.3. Control
18.4. Project Quality Control
18.4.1. Project Quality
18.4.2. Project Quality Costs
18.4.3. Importance of Quality
18.5. Project Quality Management
18.5.1. Planning of Quality Management
18.5.2. Quality Management
18.5.3. Control
18.6. Quality: Nonconformities in Project
18.6.1. The Importance of NCs
18.6.2. Customer Nonconformities
18.6.3. Contractor Nonconformities
18.7. Project Stakeholder ManagementÂ
18.7.1. Stakeholder Expectation Management
18.7.2. Interpersonal and Team Skills
18.7.3. Conflict Management
18.8. Project Stakeholder AnalysisÂ
18.8.1. Identifying Stakeholders
18.8.2. Engagement Planning
18.8.3. Management and Monitoring Engagement
18.9. Project Integration ManagementÂ
18.9.1. Development of the Project Charter
18.9.2. Development of the Project Management Plan
18.9.3. Direction and Management of Project Work
18.10. Project Integration ControlÂ
18.10.1. Project Knowledge Management
18.10.2. Work Control
18.10.3. Integrated Change Control and Project Closure
Module 19. Project Management in Projects: Purchasing and Resource Management
19.1. Control of Purchases
19.1.1. Project Purchases
19.1.2. The Buyer
19.1.3. The Supplier
19.2. Project Purchase Cycle
19.2.1. Analysis of Purchase Cycle
19.2.2. Stage Description
19.2.3. Stage Study
19.3. Purchase Contract
19.3.1. Elements of the Contract
19.3.2. Contract Terminology in Contract
19.3.3. Control of Claims and Litigation
19.4. Project Purchase ManagementÂ
19.4.1. Types of SuppliersÂ
19.4.2. Procurement CategoryÂ
19.4.3. Types of Contracts
19.5. Project Purchase AnalysisÂ
19.5.1. Purchasing Management Planning
19.5.2. Execution of Purchases
19.5.3. Control of Purchases
19.6. Resources Control
19.6.1. Project Resources
19.6.2. Conflict Management Skills
19.6.3. Levels of Conflict and Resolution
19.7. Management of Resources by Objectives
19.7.1. Management by Objectives (MBO)
19.7.2. Different Roles in the Projects
19.7.3. Types of Leadership
19.8. Project Resource ManagementÂ
19.8.1. Resources Management Planning
19.8.2. Estimated Resources of the Activities
19.8.3. Obtaining the Necessary Resources
19.9. Project Resource AnalysisÂ
19.9.1. Resource Team Development
19.9.2. Team ManagementÂ
19.9.3. Equipment Control
19.10. Analysis of the Resource Interview Process from the PM
19.10.1. Interview Process
19.10.2. Analysis by the Project Manager
19.10.3. Factors to Consider for a Successful Result
Module 20. Project Management in Projects: Resource Management
20.1. Cost Control: Project Margin
20.1.1. Project Costs
20.1.2. Calculation of Initial Margin
20.1.3. Financial Control
20.2. Cost Control: Cash Flow
20.2.1. Analysis of the Projects Cash-Flow
20.2.2. Production
20.2.3. Factors
20.3. Activity Cost Estimation
20.3.1. Cost Estimation Techniques
20.3.2. Factors in Favor and Against the Estimation of Activities
20.3.3. Aspects a Take into Account in the Estimate of Costs
20.4. Project Earned Value Management and Control
20.4.1. Basics of Earned Value
20.4.2. Processes
20.4.3. Project Control and Importance
20.5. Control and Management of Project Earned Term
20.5.1. Basics of Earned Term
20.5.2. Processes
20.5.3. Project Control and Importance
20.6. Project Cost Management   Â
20.6.1. Plan
20.6.2. Cost Estimation
20.6.3. Determination of the Budget
20.7. Project Cost AnalysisÂ
20.7.1. Cost Control
20.7.2. Production Control
20.7.3. Cost Analysis Vs. Production
20.8. S-Curve Management in the Project
20.8.1. Fundamentals about the S-Curve
20.8.2. Management Processes
20.8.3. Importance of the S-Curve
20.9. S-Curve Control and Elaboration in the Project
20.9.1. Production
20.9.2. Monitoring
20.9.3. Control and Deviations
20.10. Project Financial Study
20.10.1. NPV- Net Present Value
20.10.2. IRR-Internal Rate of Return on Project
20.10.3. Payback- Payback Period
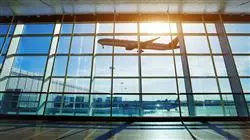
A unique, key and decisive educational experience to boost your professional development and make the definitive leap"
Advanced Master's Degree in Senior Management in Industrial Companies
Industrial companies represent a fundamental factor for the corporate sector, as they are responsible for converting raw materials into innovative products that meet the needs of today's market. This field, like many others, is immersed in globalized environments, which drive the creation of innovative strategies to keep their operations at the forefront. This scenario demands highly qualified professionals in the management of some corporate features such as new work methodologies, tools that provide greater agility and security parameters in daily work. Based on this, TECH Global University developed its Advanced Master's Degree in Senior Management in Industrial Companies, a prestigious postgraduate program, created with the highest academic standards. The program has a 100% online mode of study and is composed of didactic resources that will give a plus to your educational experience. During two years, you will have a unique syllabus, carefully designed by a team of experts, where you will find aspects such as the integration phases of a project, the optimization of logistics functions, Lean Manufacturing and production planning that maintain profitability in the company. As a result, you will master the strategic keys that improve the performance, competitiveness and evolution of the company.
Get your degree with an online Advanced Master's Degree in senior management of industrial companies
Today, corporate environments are driven by globalization, innovation and the digital era. Therefore, in this TECH postgraduate degree, we focus on providing you with the most up-to-date content to become a specialist. Here, you will find the necessary tools to diversify your knowledge and achieve high positions in the industrial companies sector. During the course of the Advanced Master's Degree, you will be continuously accompanied by experts, who will contribute their maximum experience to the curriculum. The syllabus will allow you to explore aspects such as the new business models associated with the implementation of Industry 4.0, the stages in EPC (Engineering, Procurement and Construction) projects and the management of quality, human resources and economics in the areas of the company. You will also explore all operational processes, including manufacturing control, product design, costs, logistics, communications and supply chain. Thanks to this, you will succeed in planning innovative strategies that keep operations active in the company.